Unlocking Autonomy and Growth: The Impact of Laser Cutting Technology in Metalworking
VOSSE: A History of Excellence
Vosse's story begins with the deep-rooted legacy of Wandtke Grupa, founded over three decades ago by Mieczysław Wandtke. Following his father's steps, Kamil Wandke took over the already successful business and established Vosse.
Since then, the company has constantly evolved by investing in new technological solutions to offer a wide range of steel products based on certified quality management systems.
With more than 30 years of experience, 1,800m2 of production space, and over 300 clients, Vosse provides steel structures for the construction and automotive industries to meet the highest level of quality required by its customers around the world.
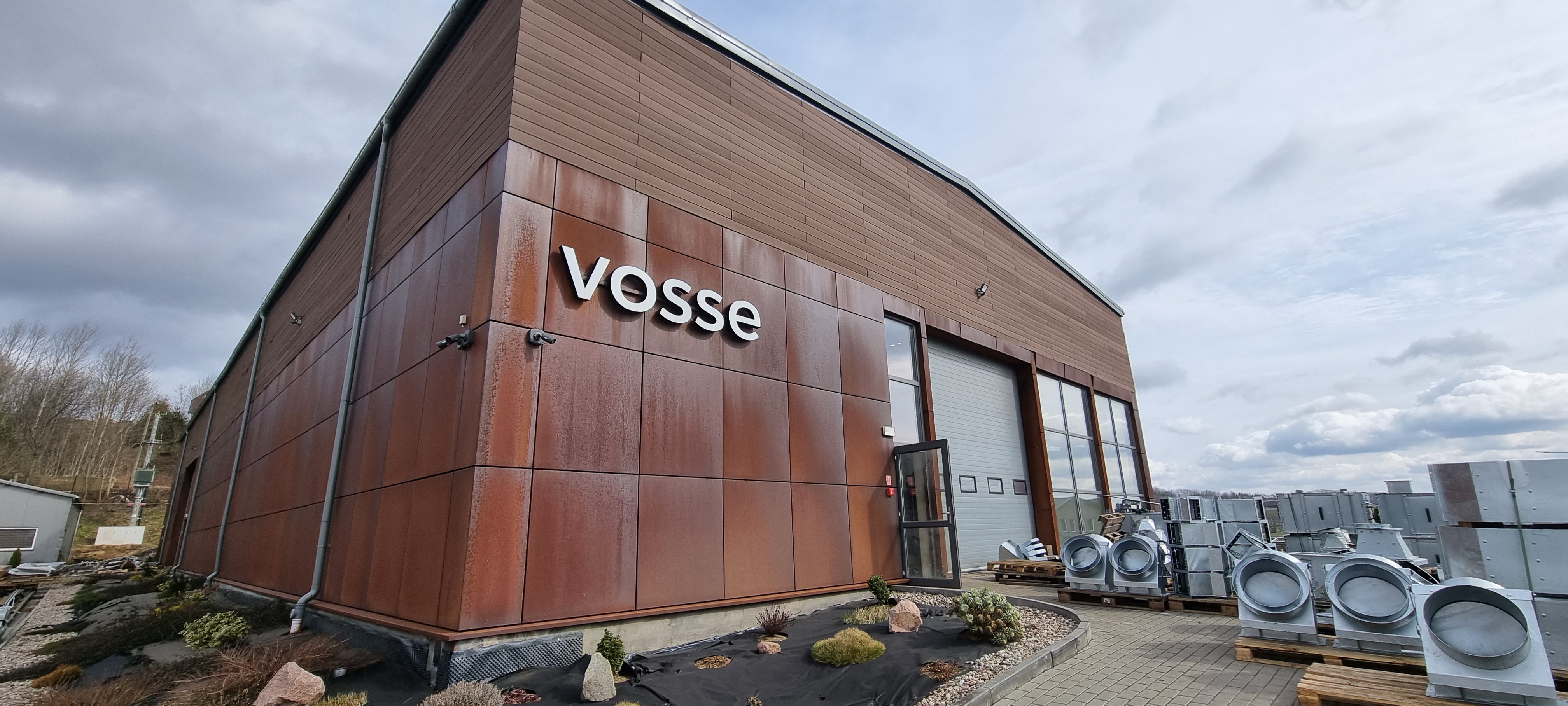
A Quest to Gain Process Autonomy
As Vosse's scope of services widened, the need for greater control and efficiency became evident. Up to two years ago, the company had been outsourcing laser-cutting processes, which led to extended deadlines, increased transport expenses, and more complex logistics.
"It was simple maths; we calculated our annual expenses and contrasted them with those of leasing a laser. Continuing as a cooperative business became impractical. It was high time we bought a laser cutting system." comments Robert Gołębiewski, CEO at Vosse.
Having the laser-cutting machine in-house has significantly impacted Vosse's operations. Not only does it provide them with greater control but it also prevents the common time lags associated with external suppliers and allows the company to better adapt to seasonal fluctuations.
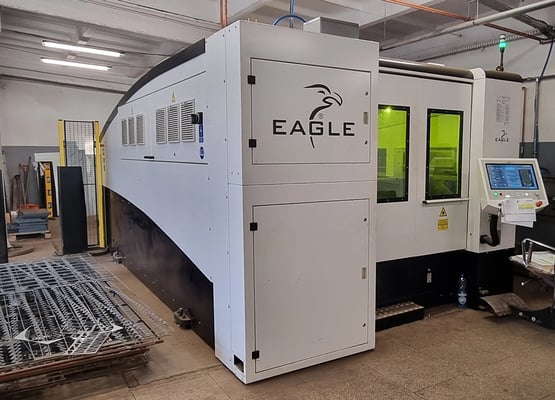
"Production is a living organism. It's constantly changing, and when relying on external sources, those changes often meant new orders. That was a huge problem for us", adds Gołębiewski, who also mentions there's a perception factor to be acknowledged when acquiring a new machine:
"A company looks much different having a fiber laser cutting machine in its ranks. It's a modern machine park and this can be decisive for some customers."
Choosing the Right Manufacturer
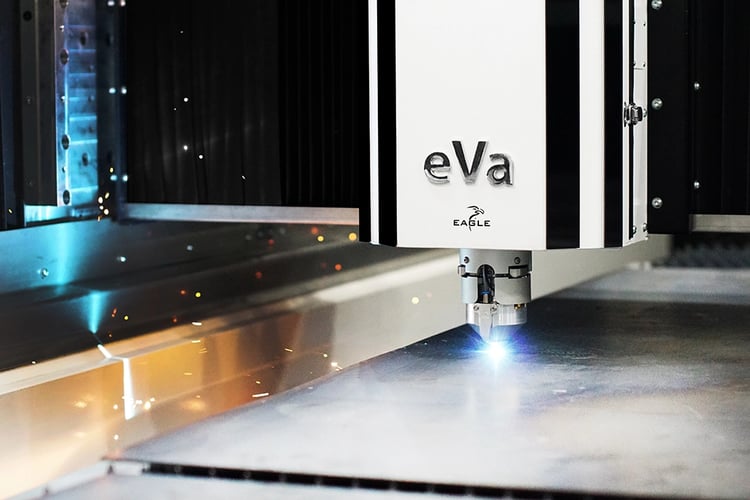
When the decision to purchase a fiber laser cutter was settled, the time came to choose one suited to the company's needs and requisites.
Vosse evaluated several top-tier manufacturers by visiting trade shows and carefully analyzing machine features but, above all, by performing cutting tests with different devices using the exact same materials and parameters.
When the test was executed at Eagle's headquarters, the cut sample proved superior, and the answer was clear. In Gołębiewski’s words:
"We made the final decision based on the tests performed at Eagle's headquarters in Wałcz. Additionally, as a Polish company, they aligned with our objective of supporting local businesses."
As for the machine model, one of the primary considerations was the range of sheets the machine could handle. To determine this, they examined their project history and anticipated the type and size of materials to be processed. The highest volume of sheets Vosse processes is 1.5m x 3m; hence they opted for a 6kW Eagle eVision 1530.
The Key to Expansion
Having Eagle's eVision in-house has been a game-changer for Vosse these past two years. By cutting the middleman, they drastically reduced transport costs and logistics issues and were able to start producing what have become some of their most in-demand orders.
"With this modern machine park, our company has transformed, allowing us to operate independently and expand our potential. We have completed new projects involving cutting aluminum scaffoldings; we started producing a variety of smaller steel parts and, thanks to the fiber laser machine, we are now also manufacturing building facades," comments Gołębiewski
Currently, the Eagle eVision operates in two shifts, and Vosse doesn't rule out the possibility of including a third in case the workload keeps growing.
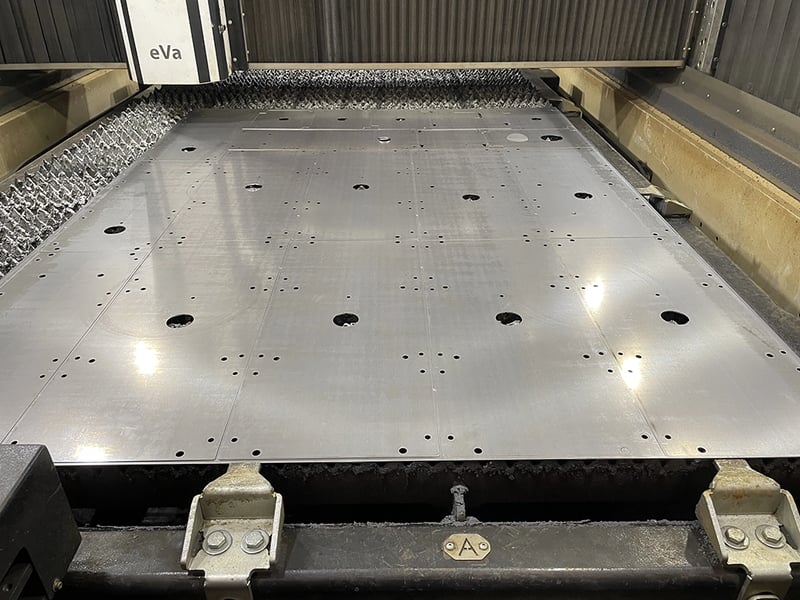
Exceeding expectations
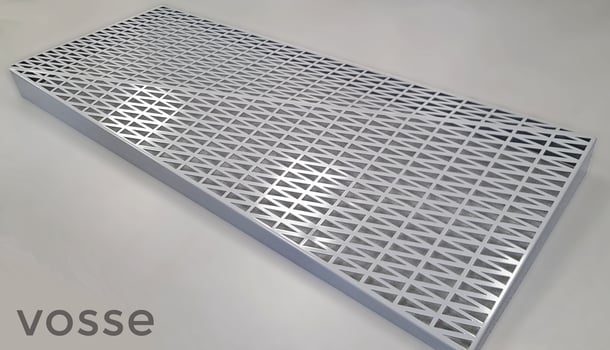
"The quality and speed exceeded our expectations. The machine is also very user-friendly, and the employees new to fiber laser technology quickly grasped how to operate it. The support provided by Eagle's service team was also commendable, not to mention the organization of the whole process, which was outstanding from the very beginning," says Gołębiewski.
Plans for the Future
Product-wise, they will continue to amplify their portfolio by producing their own line of pole cranes, and this might just be the beginning.
The decision to invest in laser cutting technology has transformed Vosse's metalworking operations, enabling faster turnaround times, significant savings, and a broader range of manufactured products.
"At the moment, we don't run laser cutting services, we only use the machine for our production, and it's still heavily loaded. It's satisfying and shows what an accurate purchase this was," adds Gołębiewski.

With a focus on continuous growth and innovation, Vosse remains a leading force in the metalworking industry, leveraging the power of laser cutting expertise to deliver exceptional results.
If growth continues at this pace, they might need a second machine, and as Gołębiewski tells us, their positive experience with the eVision will make that choice an easy one:
"For me, this machine works sensationally well. We haven't had any issues with it, so if I were to consider buying a second laser cutter, it would be Eagle."