Vergeest Metaaltechniek - 300 Years of Dutch Excellence Ferried into the Future Together with Eagle
A family tradition turned into an international success
Dutch company Vergeest Metaaltechniek has a rich history dating back to 1726 when it originated as a blacksmith shop. Over the centuries, a strong family tradition of craftsmanship has been created, with expertise passed down through generations.
Today, Vergeest Metaaltechniek prides itself on offering comprehensive 2D and 3D sheet metal solutions to its clients. From technical design to laser and plasma cutting. Furthermore bending, welding, sawing and drilling. They also provide services for electrolytic galvanizing, hot dip galvanizing, zinc-nickel coating, powder coating, and wet painting. The company also offers transport services, with everything done in-house, from design to delivery!
“We launched the company with my wife Monique 30 years ago. We initially started operations at the old location in Hernen, and then relocated to Wijchen in 2003”, says Joris Vergeest, Vergeest’s co-owner & Managing Director. “Initially, we constructed 1,000m², then doubled those, and subsequently added another 1,200m². Bringing our total workspace to 3,200m². The premises are energy neutral, running on 750 solar panels”.
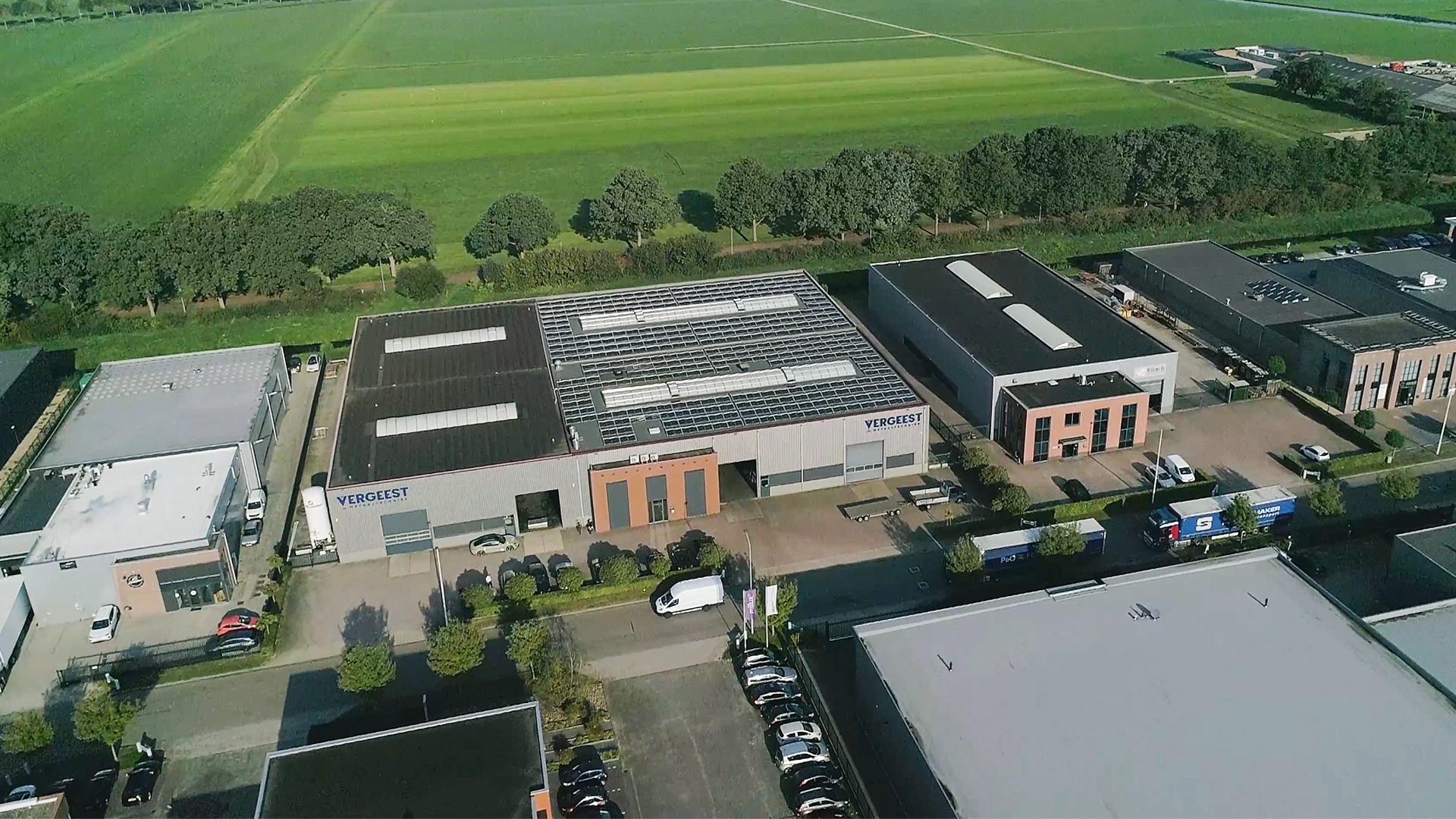
Heavy-duty machines for heavy-duty work
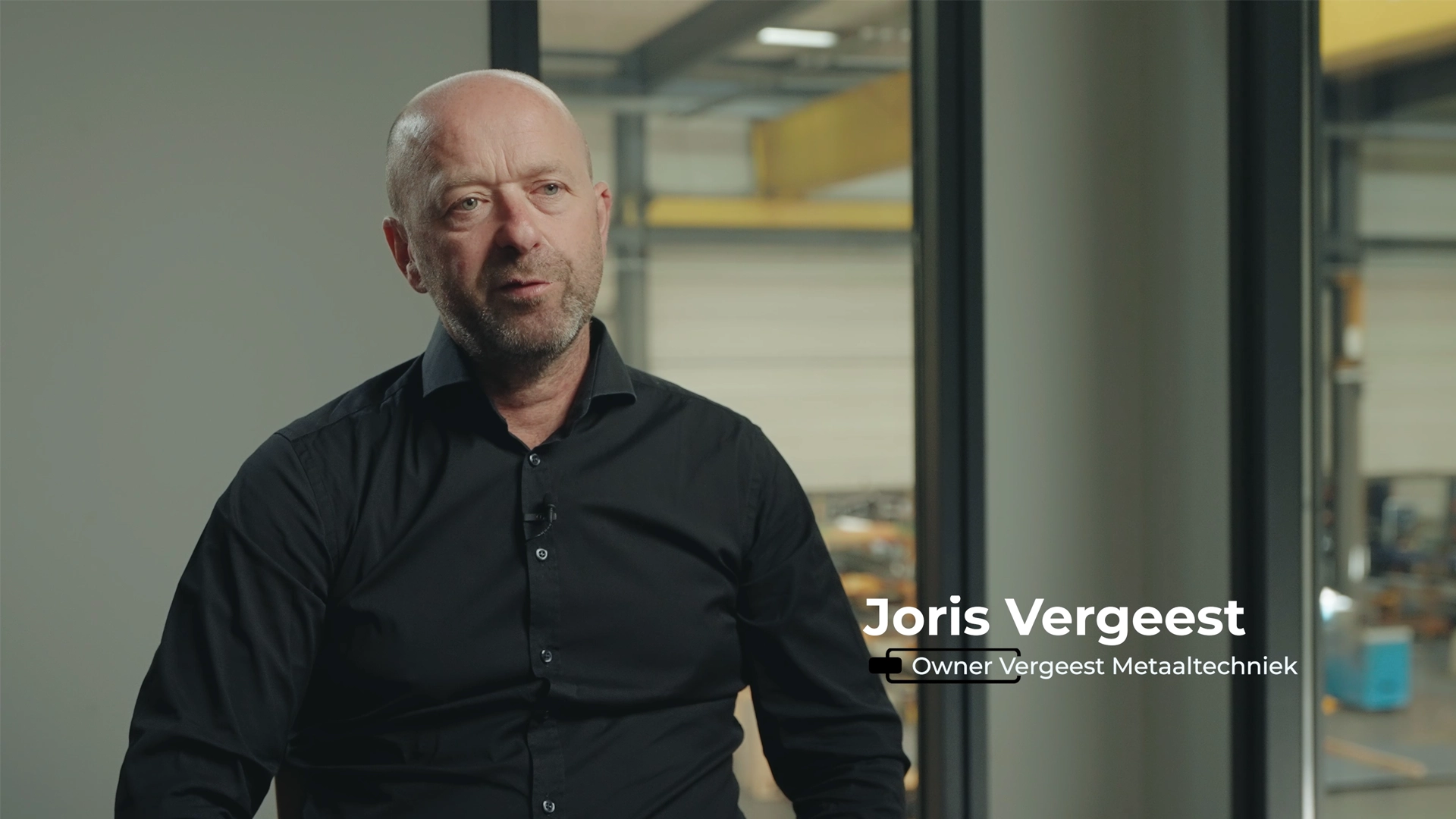
“Our primary focus in production is supplying components for the trailer building industry. Additionally, we serve the offshore sector and produce components for excavators. We began our cutting operations with a pre-owned CO2 machine, a 2.5KW model that served us well for about five years. However, as we thought to enhance our capabilities, we explored fiber laser cutting technology. We ultimately chose an Eagle iNspire 1530 15kW with the Crane Master Store Extended automation system”, tells Joris.
“Our decision was driven by the realisation that with a lower-power laser, competing effectively becomes challenging due to limitations in cutting speed and quality. This, in turn, leads to high fixed costs that cannot be offset by reducing hourly rates without compromising profitability. Therefore, upgrading to a more efficient laser system was a strategic move”.
Vergeest’s primary material for fabrication is mild steel, with thicknesses ranging from 3mm to 30mm. While 2mm is the minimum thickness they typically work with, the majority of their projects involve sheets starting at 3mm, commonly utilising grades such as S235, S420, S700 as well as various types of Hardox.
Eagle's approach to optimisation and performance
“Mild steel comprises approximately 95% of our fabrication work”, adds Joris. After seeing an Eagle machine at the Hannover trade fair, We were particularly impressed by the eVa Cutting head: “Eagle's approach, with a large lens surface and high cover glass postion, appealed to us greatly. This design allowed for better heat dispersion, which we saw as a crucial advantage in maintaining optimal performance”.
“Unlike most companies that start with the laser source and then move to the sheet, Eagle began by considering the sheets we worked on the most and then analysed backward to the laser source. This unconventional approach demonstrated a thoughtful and thorough understanding of the cutting process”.
Joris also liked what he saw in terms of simplicity: “Especially the construction with a polymer concrete frame and the traverse made of carbon fiber. Furthermore, feeling the family character within Eagle is also important to us. We sense a family-oriented drive within the company, which resonates with us deeply”.
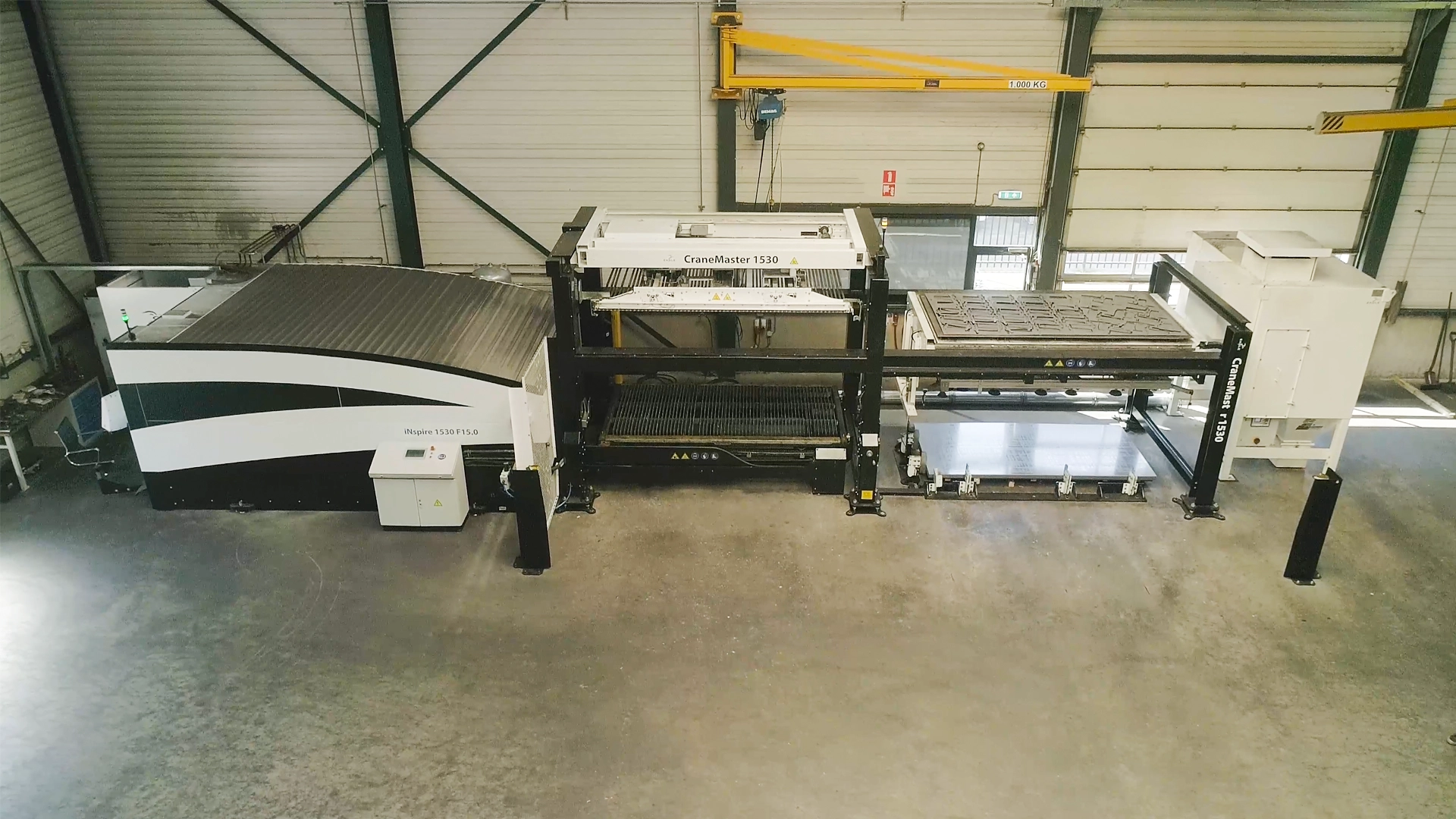
Fast installation, faster turnaround
“Ultimately, I realised that acceleration is also crucial, especially when dealing with extensive cutting plans containing numerous holes. The ability to exchange sheets in just 9 seconds is also a major advantage. Compared to the typical exchange time of 30-40 seconds, this swift exchange significantly boosts productivity and streamlines our operations”.
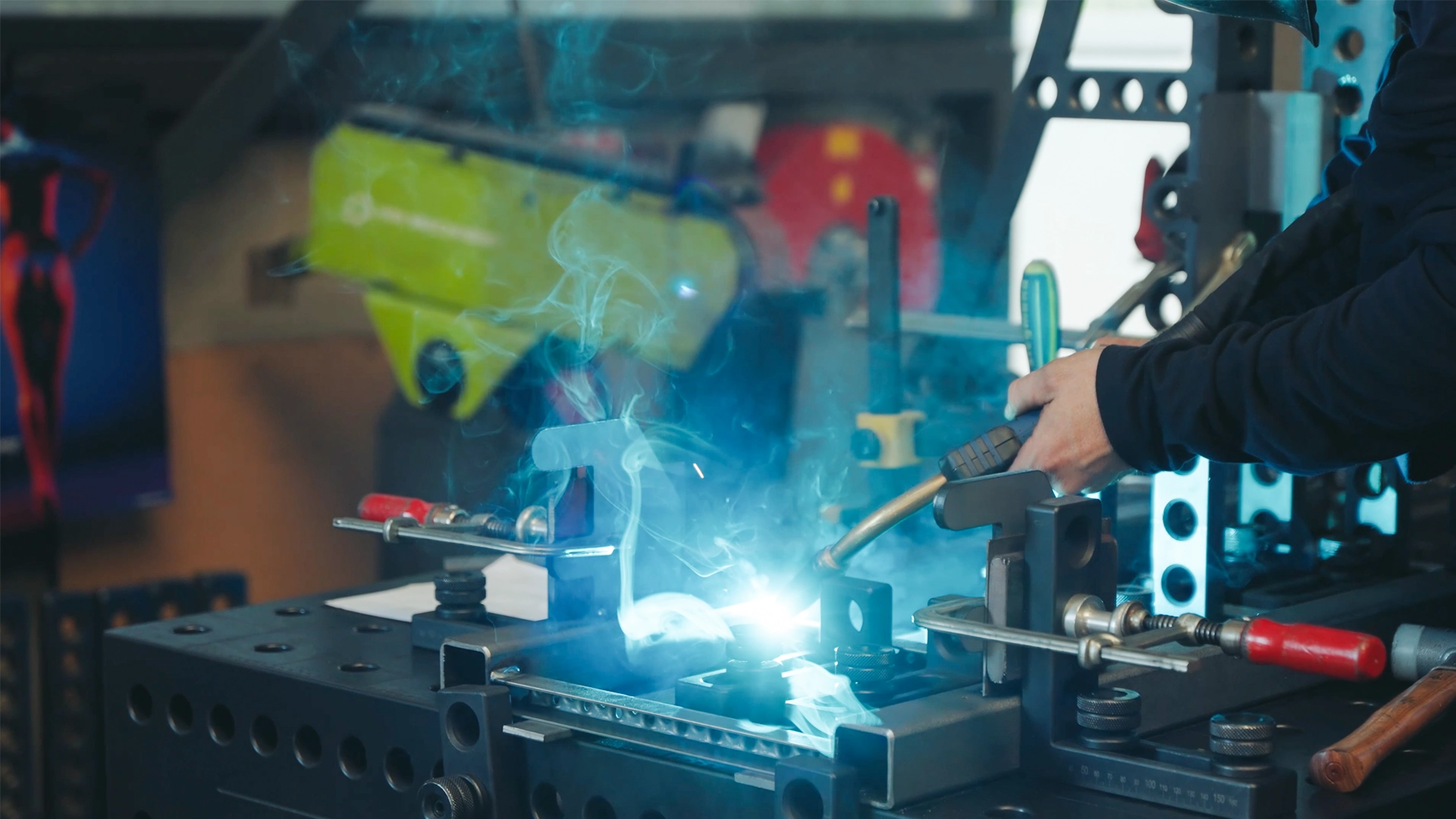
“The entire unit was delivered as one piece and unloaded with a crane before being wheeled into place on rollers. I recall the installation taking only 2-3 days, after which the machine was operational. In the first year alone, we were able to break even. This investment has proven valuable for our company's success”.
Beyond technical capabilities, Vergeest prides itself on its collaborative approach, eagerly engaging with customers to develop innovative products and creative solutions tailored to their unique needs and requirements. This commitment to partnership and excellence underscores Vergeest Metaaltechniek.'s enduring legacy of craftsmanship and service.
“Our own company is built on principles of family and cohesion similar to Eagle’s, making our partnership a natural fit. We truly feel we are aligned in our values and goals, which has strengthened our bond and contributed to our mutual success”.
To meet the increasing demand for laser-cut parts, Vergeest recently opted to upgrade from the Eagle 15KW laser to the Eagle iNspire 1530 30kW model, prioritizing future capabilities for cutting thick sheets of 8 mm and above at high speed and quality. The delivery of the new laser is scheduled for August 2024.
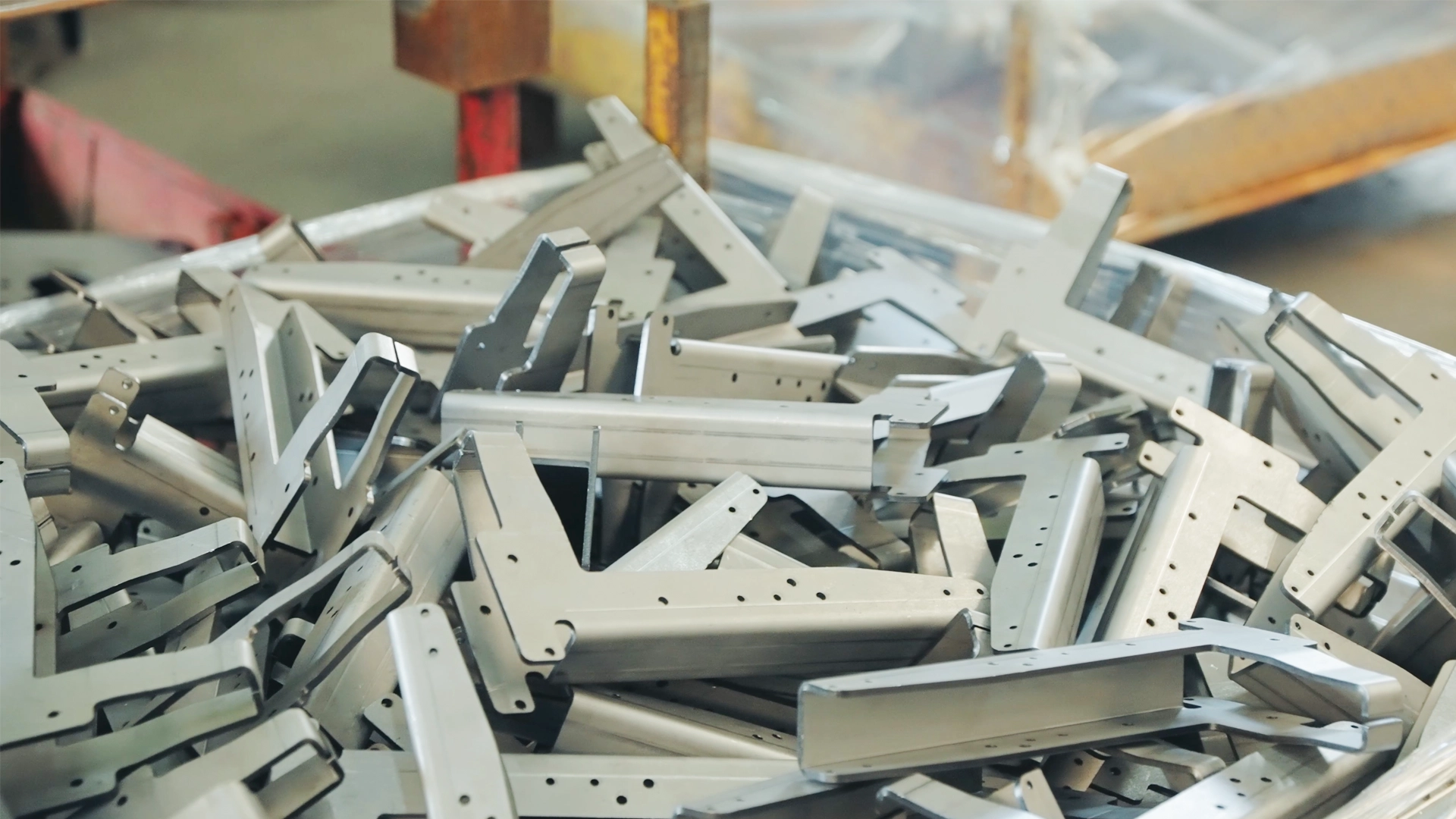