Pequea: Revolutionizing Agricultural Manufacturing with Eagle iNspire Fiber Laser
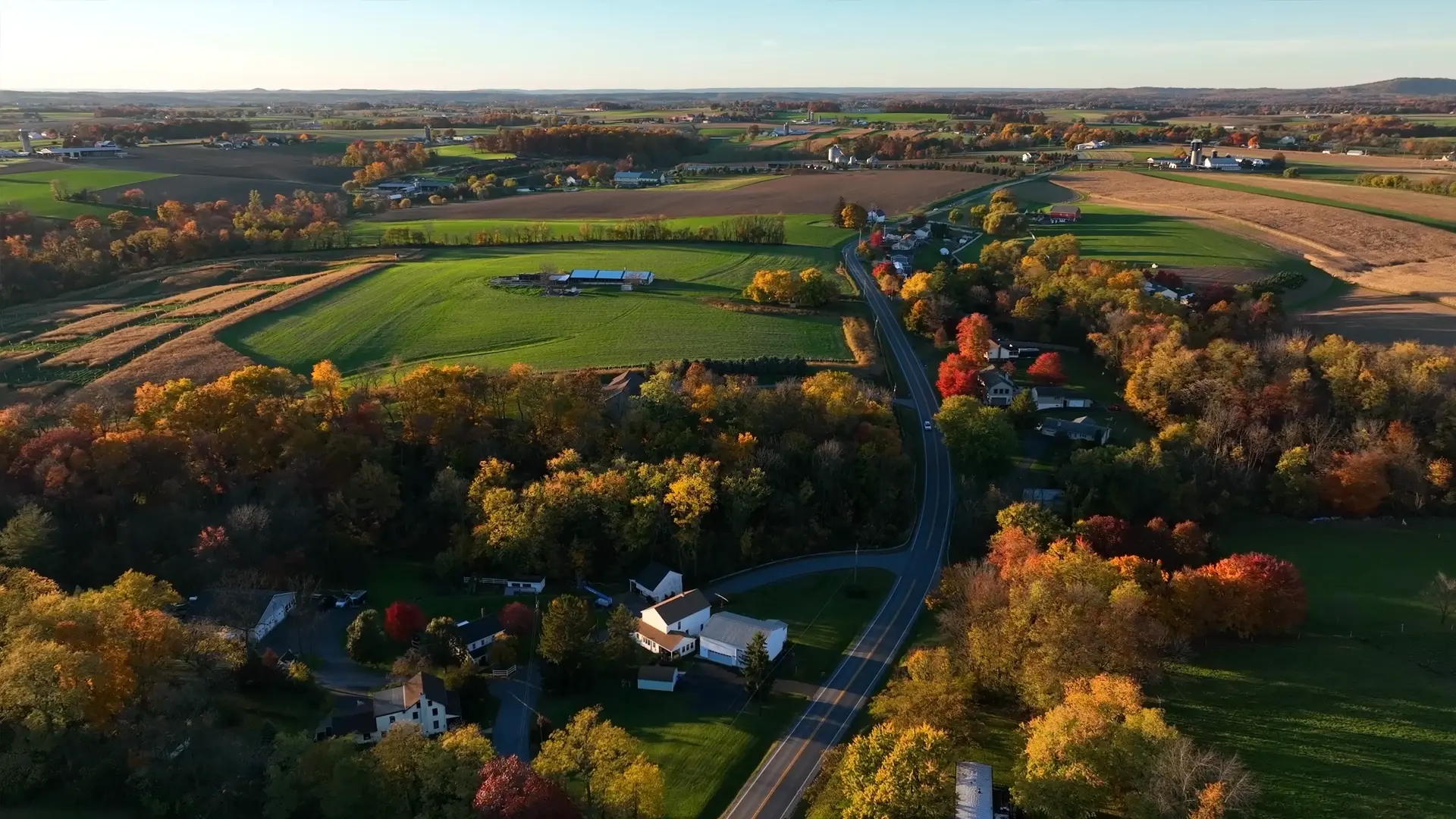
Pequea Machine’s origins are rooted in an Amish workshop in rural Pennsylvania, where it began as a family-run operation in 1970. In 1990, Dennis Skibo acquired the company and helped Pequea evolve into a leading agricultural equipment manufacturer, including hay tools, manure spreaders, and specialized vineyard and orchard machinery. By 2000, Skibo moved Pequea to a 100,000-square-foot facility that now houses 85 employees and the latest manufacturing technology.
Reflecting on the company’s journey, Skibo shares, “Taking Pequea from a small shop to where we are now involved constantly updating our tools and processes to remain competitive. Moving to fiber laser technology was one of those crucial steps forward.”
“Our main customers can be divided into two primary markets. One segment serves the dairy, hay, and cattle industries, while the other focuses on grape growers, orchards, and nut growers, including almond, pistachio, and walnut producers—primarily in the western United States, such as California, Oregon, Washington, and Arizona. Additionally, our product range meets the needs of a diverse customer base, from small hobby farmers to large commercial farms, dairies, and cattle operations. This gives a snapshot of our market reach in the field.”
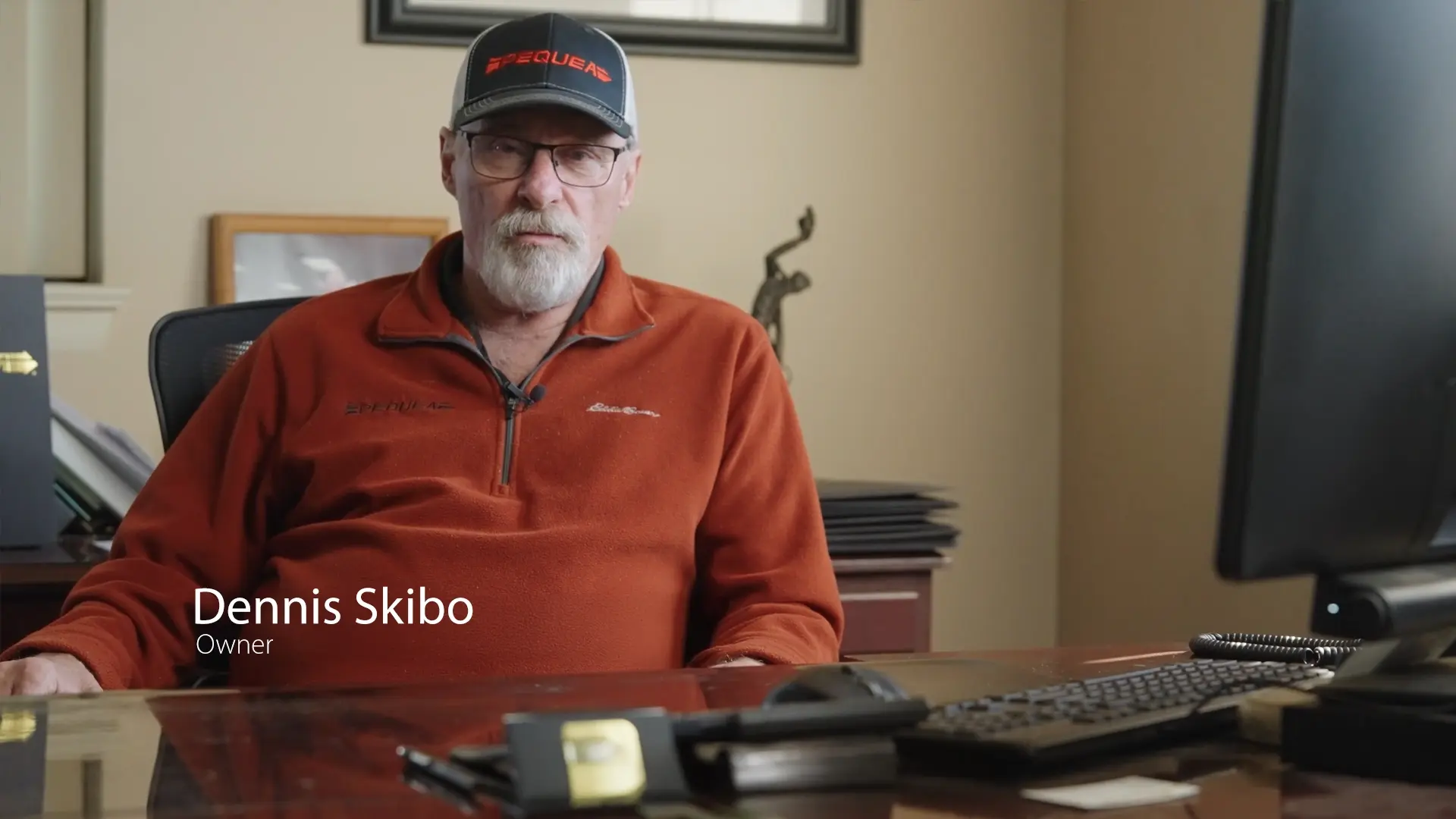
The Quest for Precision: From Plasma to Fiber Laser Cutting
Before adopting fiber laser technology, Pequea relied on a plasma cutter and outsourced laser-cut parts from local vendors. However, this combination presented challenges in terms of quality, lead times, and costs. With an eye on greater precision and efficiency, Pequea’s team explored options to meet the increasing demands of its growing business. The solution they chose was an Eagle’s iNspire 15kW fiber laser.
“The difference between plasma and the Eagle laser is like night and day,” explains Skibo. “With Eagle, we’re getting exceptional edge quality, tighter tolerances, and higher speed. The acceleration up to 6G of the Eagle means we’re effectively doubling our productivity with a single machine.”
Pequea’s investment in fiber laser cutting opened new possibilities in handling a variety of materials. The iNspire now cuts a wide range of thicknesses, from 18-gauge steel up to 1¼ inches. “I would say 75% of the parts that we cut are between 11 gauge and 3/8 thick.”
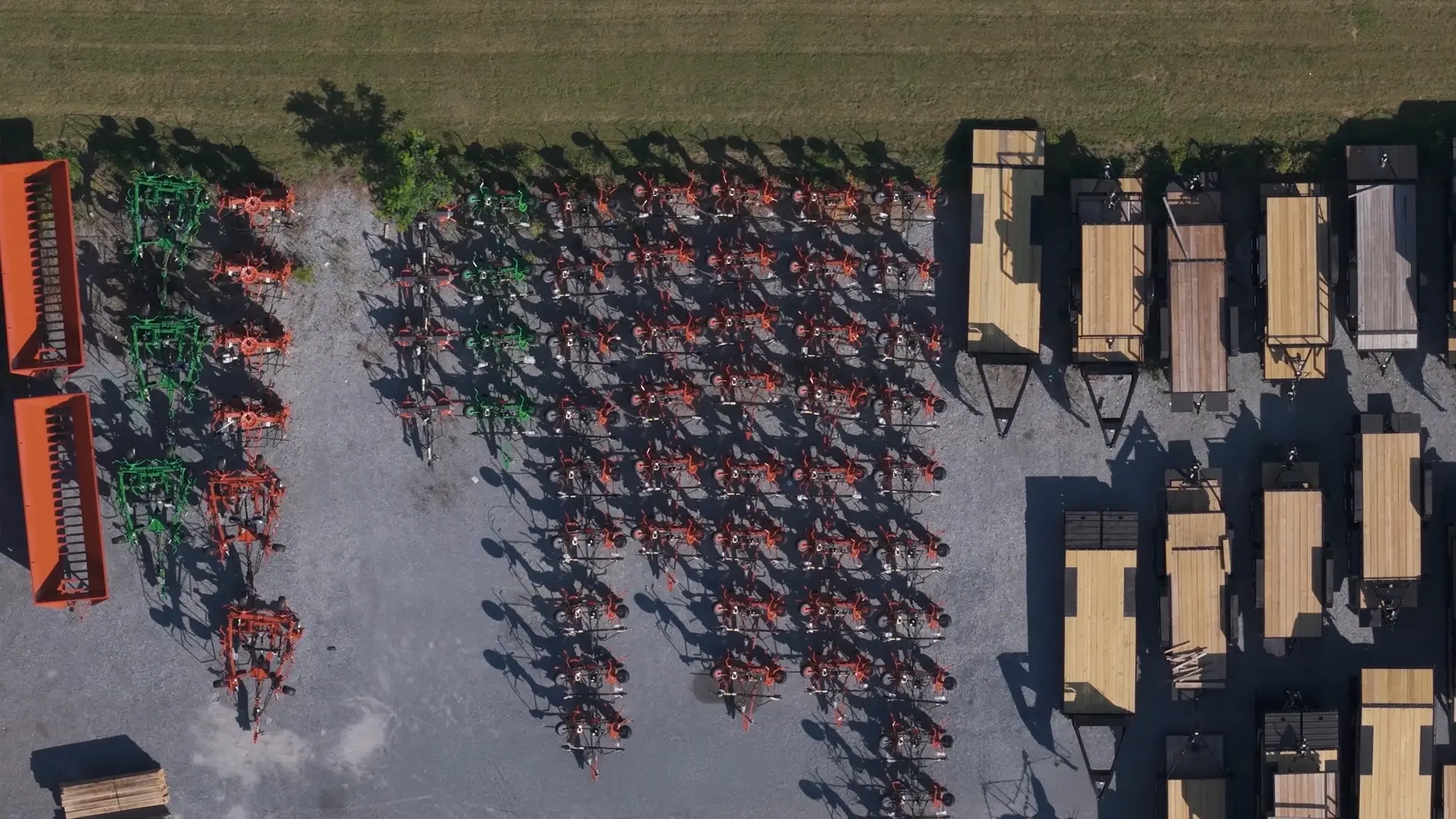
Enhanced Efficiency and In-House Control with Eagle
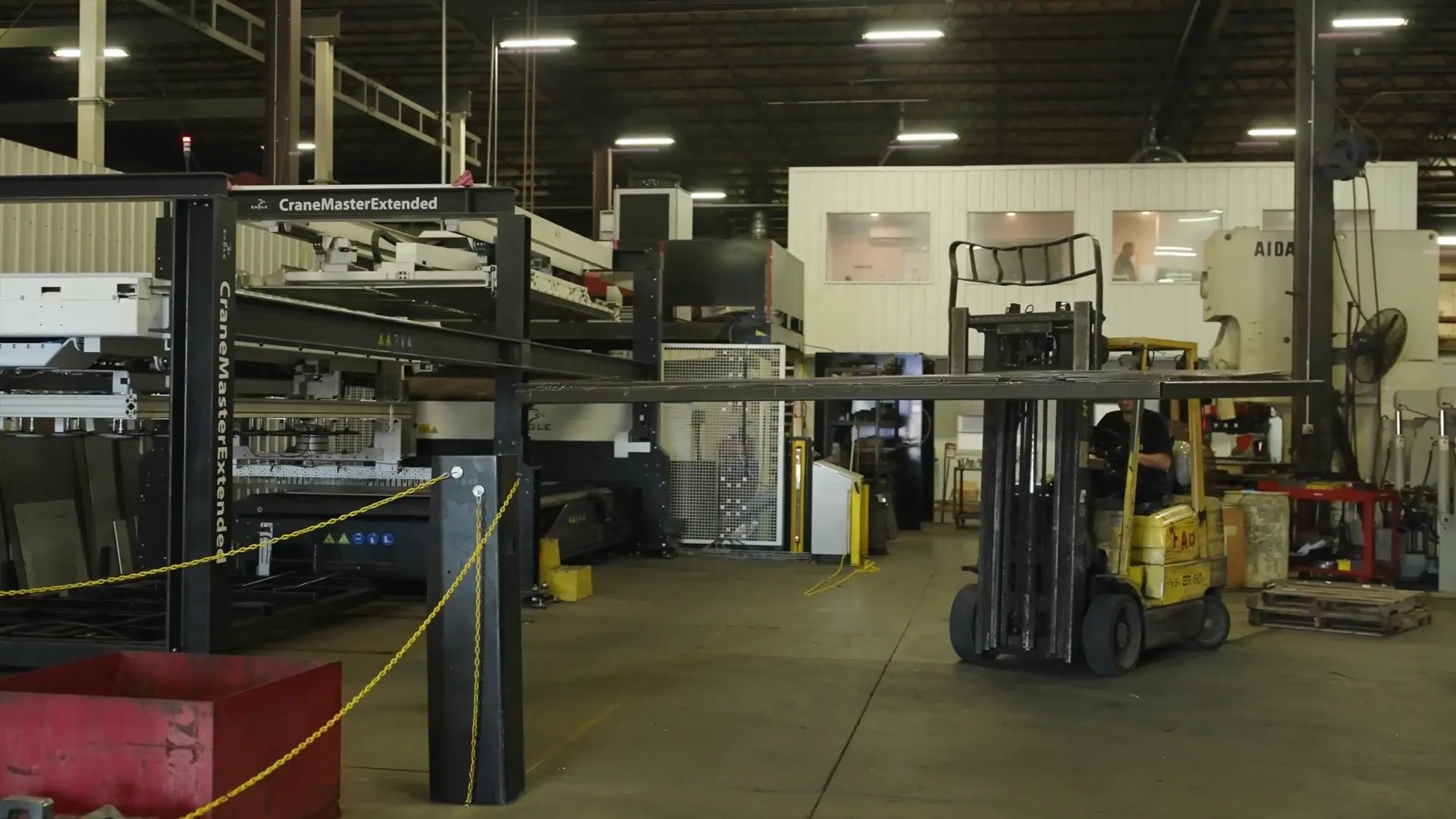
“We can cut, bend, and weld nearly all of our parts in-house now,” notes Plant Manager Jim Westlake. “This change has saved us considerable time, eliminated lead time issues from outsourcing, and improved our ability to control the quality of our work. We’ve gained the flexibility to respond to market needs almost immediately.”
The in-house laser cutting capability has also allowed Pequea to reduce inventory and streamline its production strategy. The iNspire has minimized the time required for post-processing tasks, such as edge cleaning and tolerancing for robotic welding. Westlake adds, “What drove our decision was also the nesting speed. The laser allowed us to quickly and efficiently maximize each sheet of steel, achieving high precision and minimal waste. The tight tolerances Eagle provides allow us to take full advantage of our robotic welding stations. We’re cutting labor costs significantly by reducing rework and improving assembly consistency.”
Initially, Pequea operated the Eagle laser without automation, which limited its cutting time to about 50% of the shift. However, the introduction of Eagle’s CraneMaster, an automated loading and unloading system, transformed productivity. “With the CraneMaster, we now have the machine running close to 90% of the shift,” says Westlake. “The Crane Master keeps the Eagle laser cutting non-stop, handling heavy loads, including one-inch steel plates, with ease.”
This improvement in uptime has been especially valuable for Pequea’s contract manufacturing business, where they offer cutting, welding, and bending services for other companies.
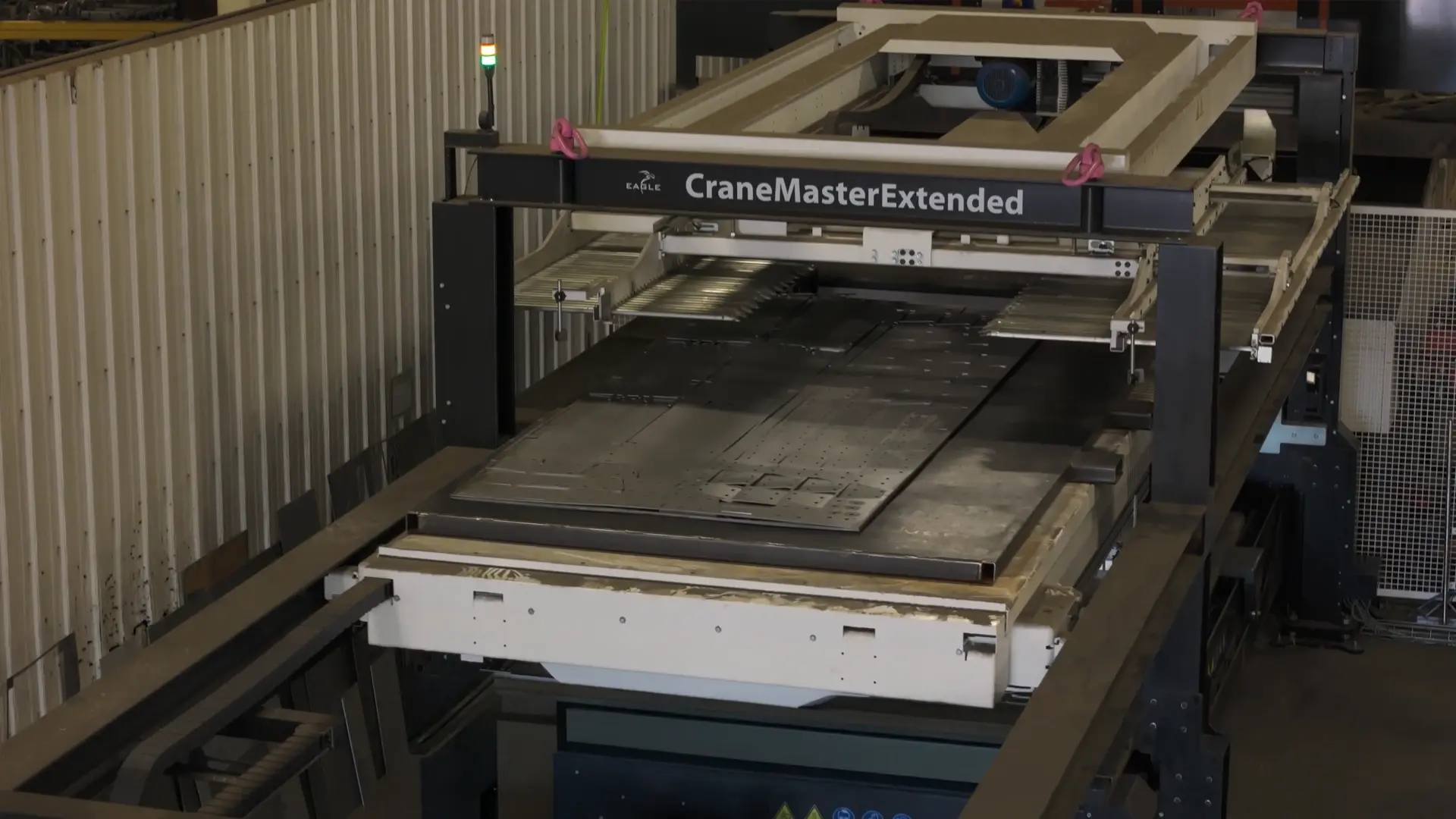
A Reliable Partner in Eagle
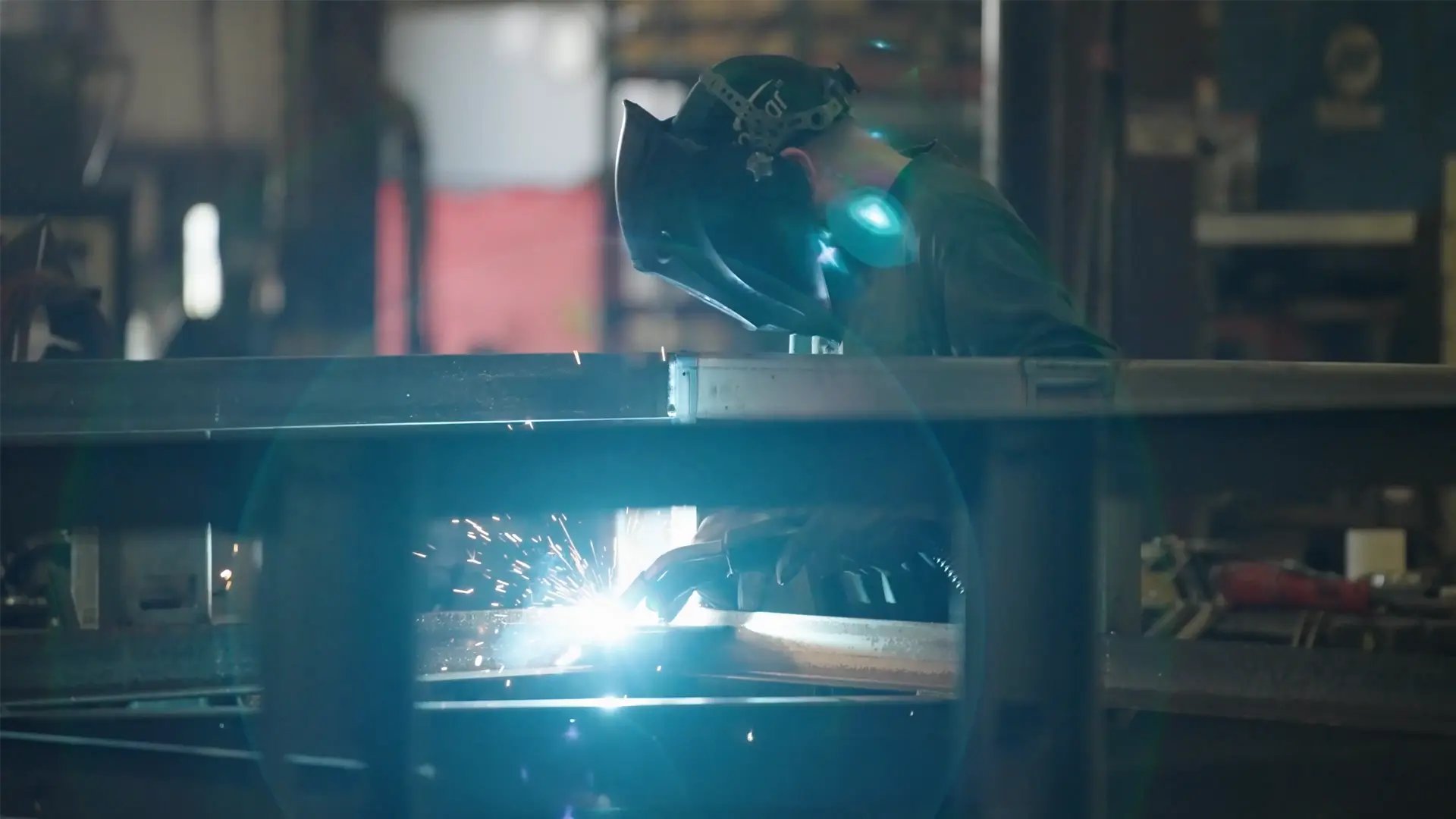
With no backup machine, reliability was critical. “We're not a laser shop; we have only one machine, so downtime isn't an option for us. Larger shops might manage a breakdown by shifting work to other machines, but we don’t have that flexibility. We needed a machine that was solid and reliable. Many other brands have poor service reputations, with repairs taking two, three, or even four days, which would be disastrous for us. So, reliability was our top priority”.
Pequea has been impressed with Eagle’s consistent support. “Eagle’s service, including remote diagnostics and rapid response, has been exemplary. Even when we had a rare issue, Eagle’s support team addressed it within hours”, says Skibo.
The Eagle Eye system allows for real-time monitoring and diagnostics, providing Pequea’s operators with an extra layer of confidence. “The Eagle Eye feature is a major asset,” says Westlake. “The team can remotely log in, monitor the laser, and address potential issues before they become problems. It’s a straightforward system that keeps us up and running with minimal fuss.”
The Eagle iNspire’s operational speed and energy efficiency have brought down Pequea’s costs considerably. While plasma cutting consumed large amounts of gas and electricity, the fiber laser operates at a fraction of those costs. “The cost reduction per part is substantial,” Westlake confirms. “It’s not just energy savings, but also labor reductions. Cutting time for some parts has been reduced to a quarter of what it was with plasma. When we’re pricing out job shop cutting, Eagle’s efficiency gives us a competitive edge in terms of both speed and profit margin.”
Pequea has seen a 4–5% reduction in production costs on certain items and has increased throughput overall. “Also: the protective lens on the Eagle is extremely durable, thanks to the distance between the cutting area and the beam’s entry point”, adds Westlake. “Our first lens lasted around nine months, even with our experimenting with different cuts and materials. We keep spare lenses on hand, but in four years, we’ve only replaced about three or four. Having experience with other lasers, I can say that this kind of longevity is rare.”
For Pequea, Eagle’s fiber laser system has been an invaluable asset in maintaining a flexible, resilient manufacturing operation that’s responsive to market needs. “We’re proud to partner with Eagle,” Skibo concludes. “The speed, precision, and reliability of the iNspire have changed the game for us. It’s a partnership that we rely on, and I wouldn’t hesitate to recommend Eagle to anyone serious about laser cutting.”
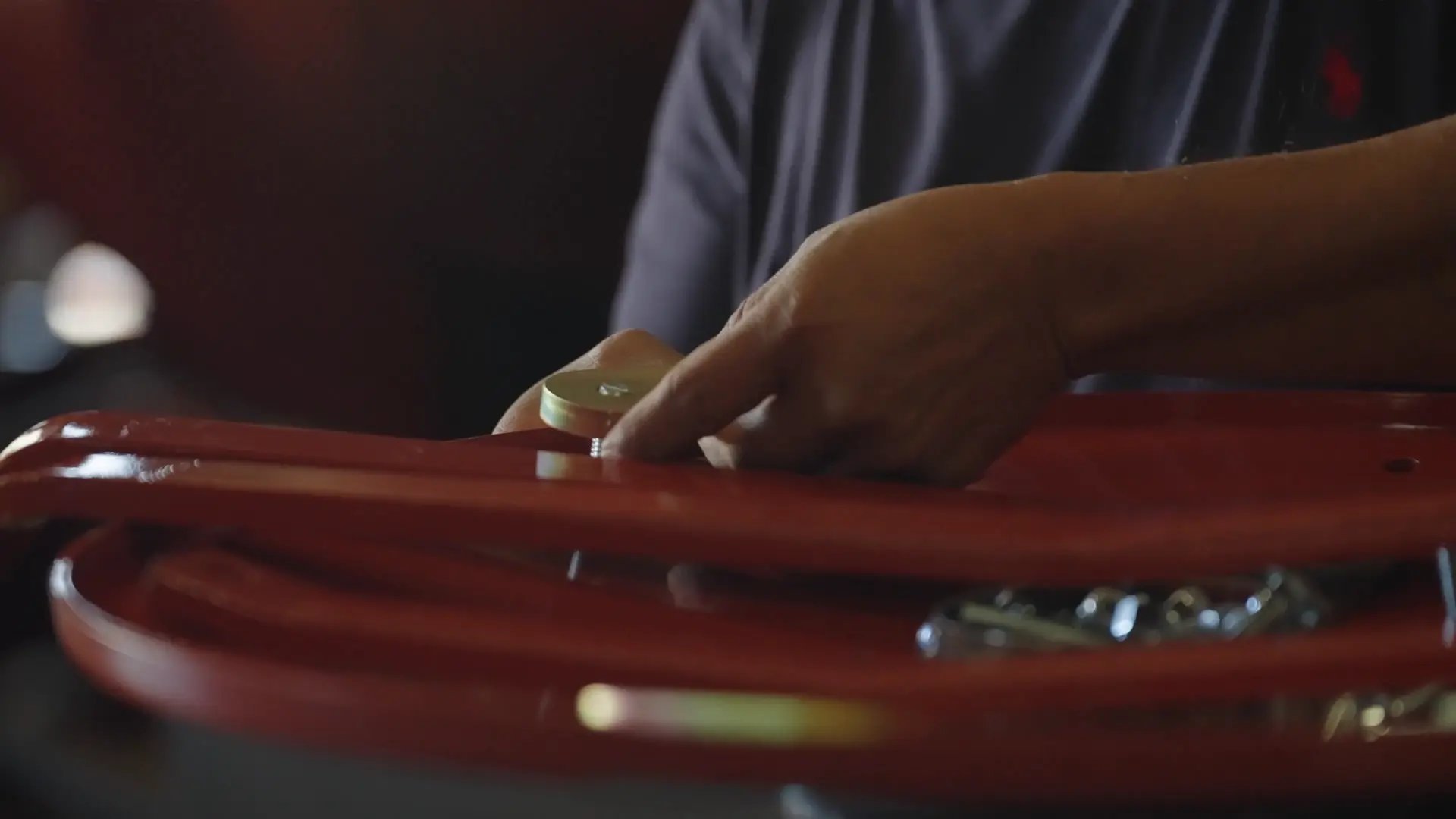