NEVA: A Quest for Higher Power, Efficiency, and Quality with Eagle
Powering Up: NEVA’s Leap into Next-Gen Laser Cutting
NEVA has been in the metalworking industry since 1998, with a clear focus on providing high-quality services right from the start. In 2013, the company moved into a new facility and began steadily expanding its operations – from laser cutting and machining to welding, powder coating, final assembly, and logistics. Today, NEVA serves both local and international clients, handling custom orders, mostly in the field of steel structure manufacturing.
The company primarily works with structural steel in thicknesses ranging from 1 mm up to an impressive 80 mm. As orders increased and the demand for processing larger formats grew, NEVA made a major move in 2021 by investing in its first Eagle iNspire 20 kW fiber laser cutting machine, equipped with a 2 × 6m worktable. This decision was driven by experience with older machines – CO₂ and low-power fiber lasers – which, while reliable, could no longer keep up with the growing need for speed, precision, and energy efficiency.
According to Tomasz Łupiński, Production Manager for the 2D laser department, the difference between CO₂ and modern fiber laser technology was immediately noticeable. The Eagle machine helped NEVA cut its energy consumption by six times. Not only did this lead to significantly faster turnaround times, but it also brought down labor costs and gave the company much-needed operational flexibility.
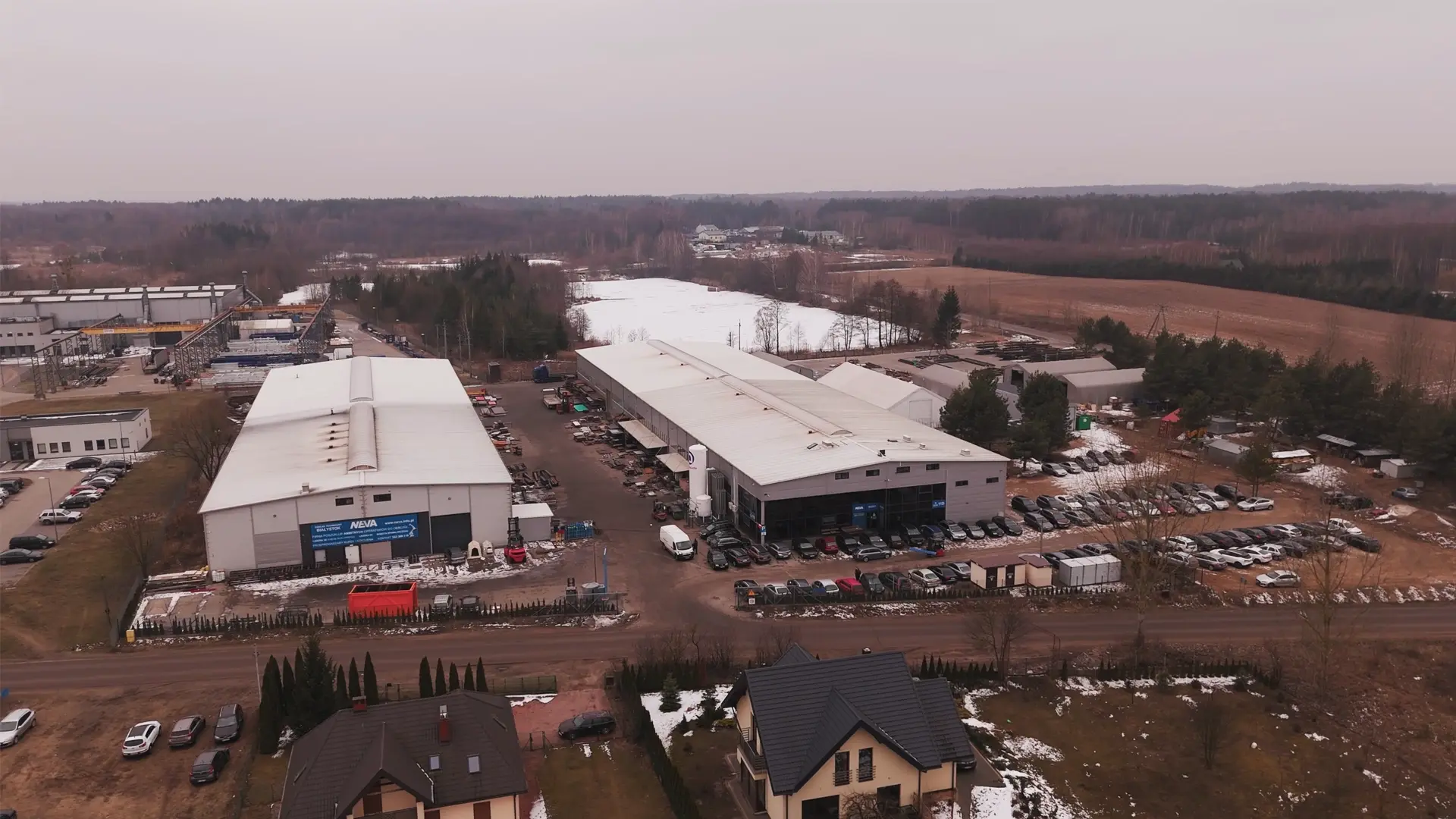
Faster, Smarter, and Built for Growth
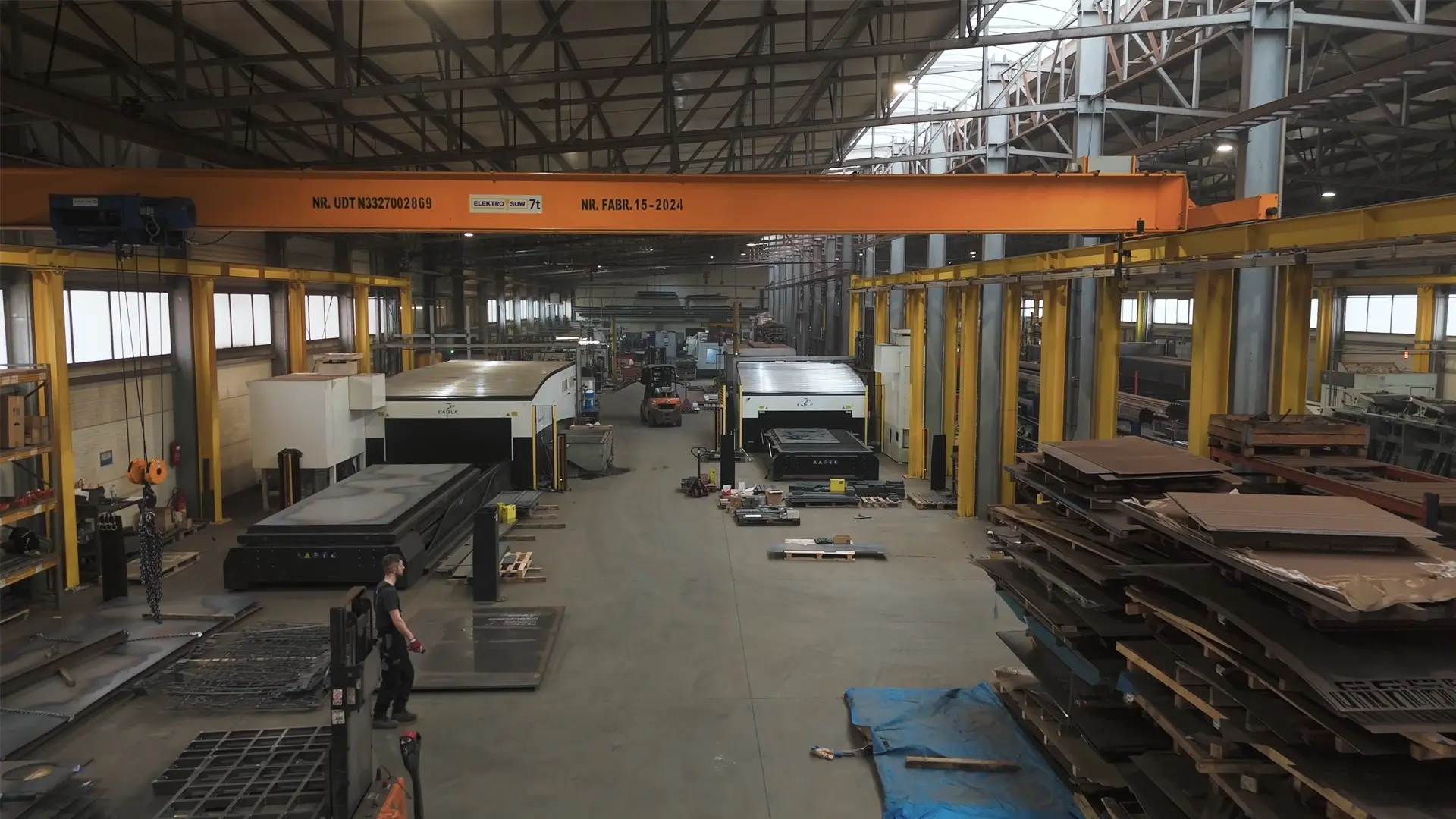
In terms of performance, the comparison was striking – the 20 kW laser could complete jobs up to several times faster than their previous 6 kW model. The larger work table also meant fewer table changes and made it much easier to handle irregularly shaped parts.
In 2024, with demand still on the rise – especially for thick sheet metal – NEVA took another big step by investing in a 30 kW Eagle laser cutter. The results were immediate: the same programs that ran on the 20 kW machine now run three times faster, without compromising on quality – in fact, in many cases, the cut quality improved. One recent project involved processing 20 tons of 80 mm thick steel, showcasing just how much power the latest Eagle technology brings to the table.
NEVA currently runs a two-shift system, with the option to expand to four shifts if needed. That’s why machine reliability and responsive service are crucial. Fortunately, Eagle delivers on both fronts – the NEVA team emphasizes how quickly and professionally technical questions and service requests are handled, calling their collaboration with Eagle’s service department “exemplary.”
If you don't see them automatically, please activate the subtitles in your language.
A Reliable Partner for the Future
Operators have also responded positively. The control panel is intuitive, the machines are safe to work with, and comprehensive training provided by Eagle helped operators improve both precision and efficiency in their daily work.
Thanks to these investments, NEVA has significantly boosted its productivity and now enjoys a clear technological advantage in the market. The company isn’t slowing down, either – plans are already underway to expand their machinery fleet and widen their service offerings.
When asked if they would recommend Eagle to others, NEVA doesn’t hesitate: "Based on our experience working with Eagle and their machines, we can confidently recommend them to anyone serious about growing their production."
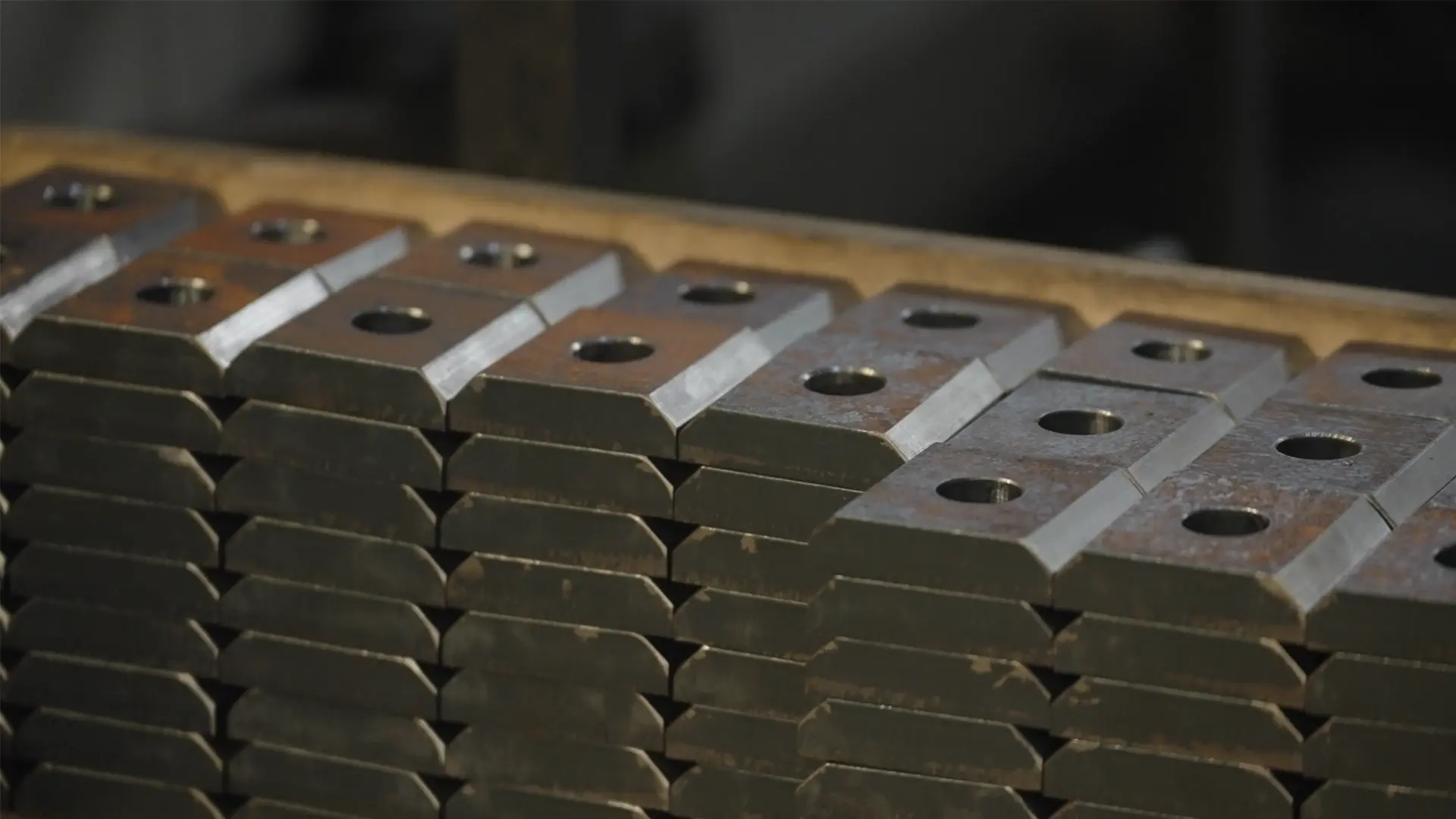