From Grapes to Lasers: The Evolution of Mildura Laser’s Business
The Early Days
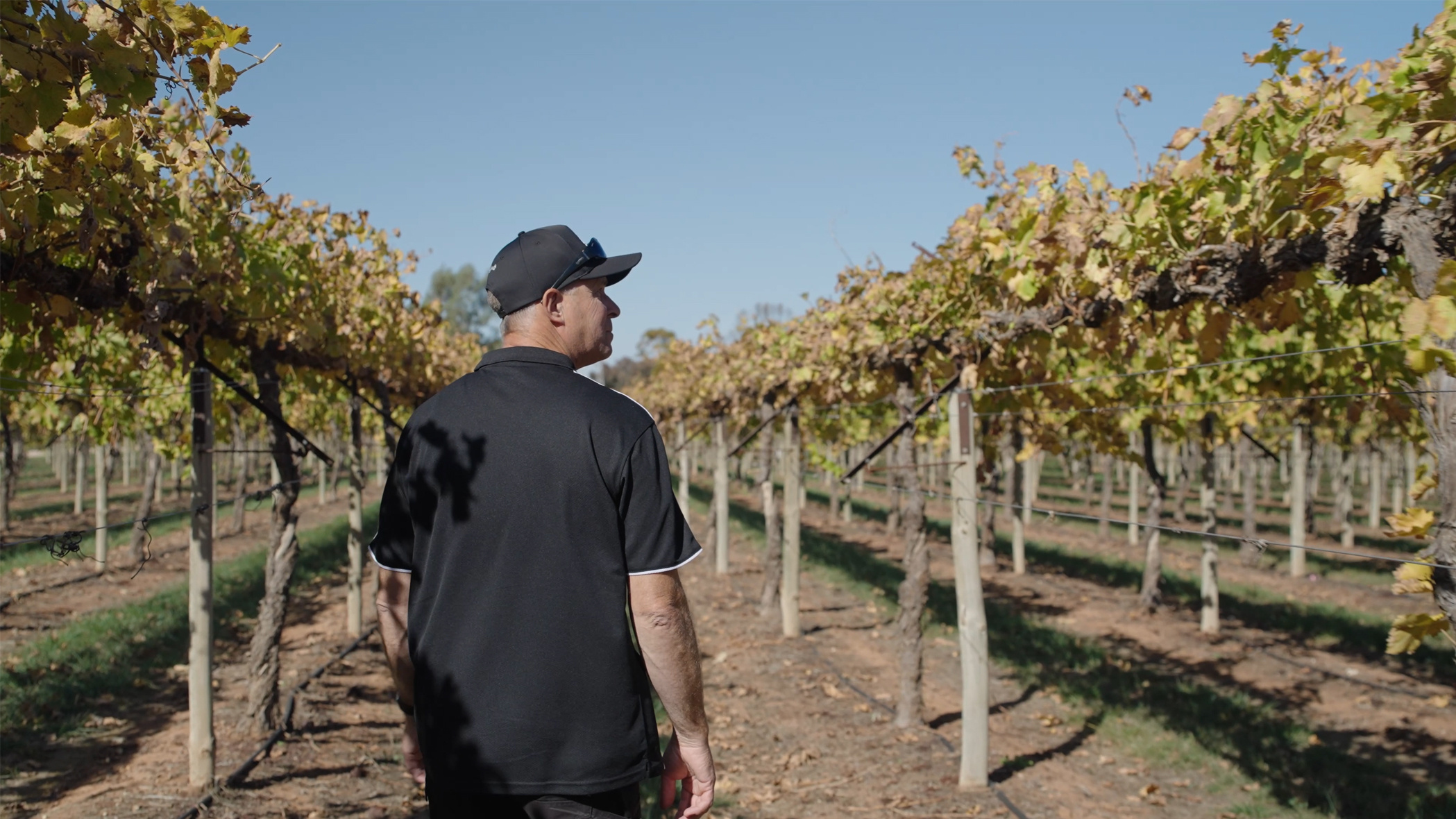
Founded in 2004, Mildura Laser, based in Northwest Victoria, Australia, and led by Rodney Trigg’s family, has steadily grown its laser-cutting business over the past decade.
Mildura Laser originally began as a trellis manufacturing business. “We bought a 10-acre property that had some grapes on it and we found a company that could make some trellis for us but they did a really poor job. So we thought, well … we can do better”, tells Rodney.
Trellis are steel V shapes that get bolted onto a post with wires running through and vines growing on those. “Ours is a big, great farming area. There's a lot of need for trellis. And that's been our core business for 20 years, as well as growing grapes. We are also involved in harvest contracting, covering 600 to 700 acres of dried fruit. We send it all over Australia and the world. We've just sent five shipping containers to the US " Rodney explains.
Ten years ago, Rodney and his team recognized a significant market opportunity. "Since trellis manufacturing and harvest contracting are highly seasonal, and since there was no laser cutter closer than Melbourne and Adelaide to Mildura, we thought we'd give it a go,” Rodney recalls. “The laser business provides a steady, year-round operation."
The journey began with an old CO2 laser. "We started with a 4kW CO2 and about five years ago, we bought an 8 kW Eagle laser," Rodney notes. "Our CO2 laser had reached capacity, running 16 hours a day, often into the night during busy weeks. We knew we needed a second laser. We decided to invest in an 8-kilowatt, which was quite large for its time, with 12-kilowatt being the biggest available. We first learned about Eagle lasers through YouTube videos showcasing their speed. Intrigued, we contacted Kraftech, the Australian dealer for Eagle. We attended EuroBLECH in Germany to see all the high-end lasers in one place. After comparing cutting times, gas usage, and other factors, we decided on the Eagle"
Since its inception, the laser business has been on an upward trajectory. "Every year it gets bigger and bigger," Rodney states proudly.
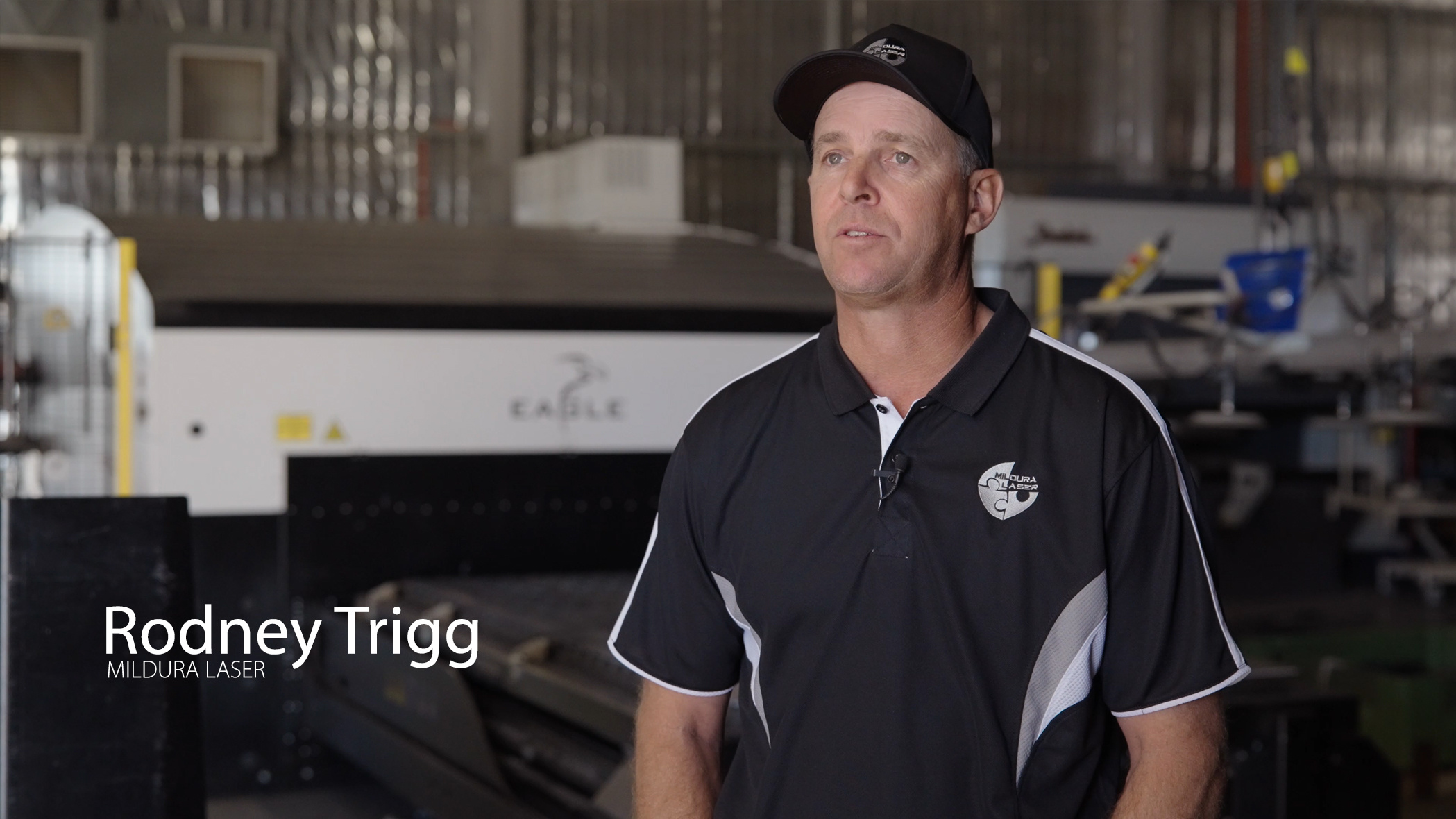
Growth and Expansion: Impact on Business Performance
The new fiber laser increased cutting speed and improved efficiency, especially for thicker materials. "The old CO2 laser struggled with these materials, but the Eagle handles them easily," Rodney says. Today, Mildura Laser serves a wide array of clients, from shed builders and machinery manufacturers to artists seeking custom pieces. The company prides itself on its ability to handle both large-scale manufacturing projects and unique, one-off creations. "We do a lot of different things, and also welding, bending, and assembling," Rodney explains.
"The Eagle laser uses less power and fewer resources compared to the CO2 laser," Rodney notes. This has allowed the company to offer more competitive pricing and quicker turnaround times. The Eagle's capability to cut up to 25mm thickness in mild steel, aluminum, and stainless steel has expanded their service offerings.
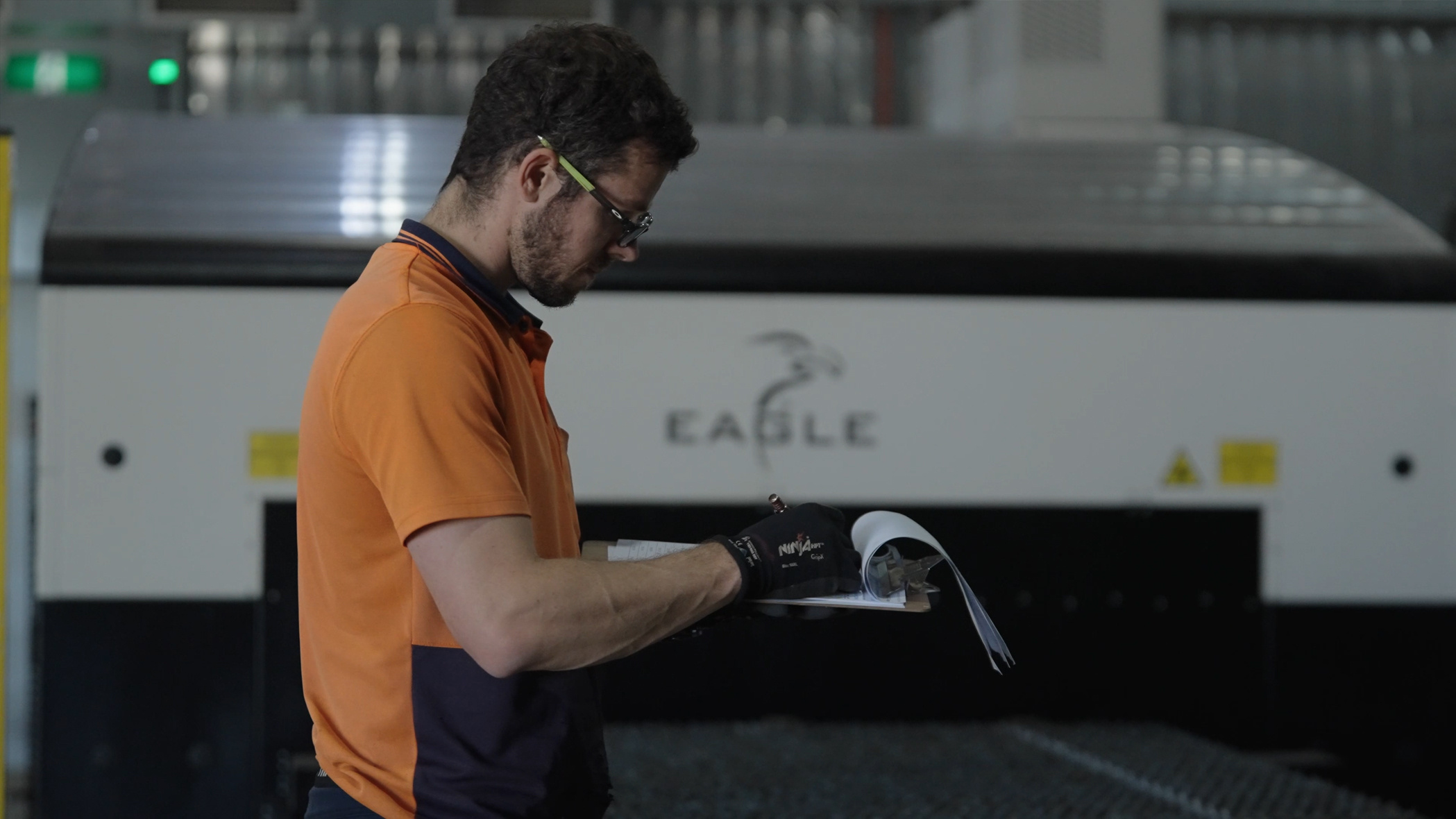
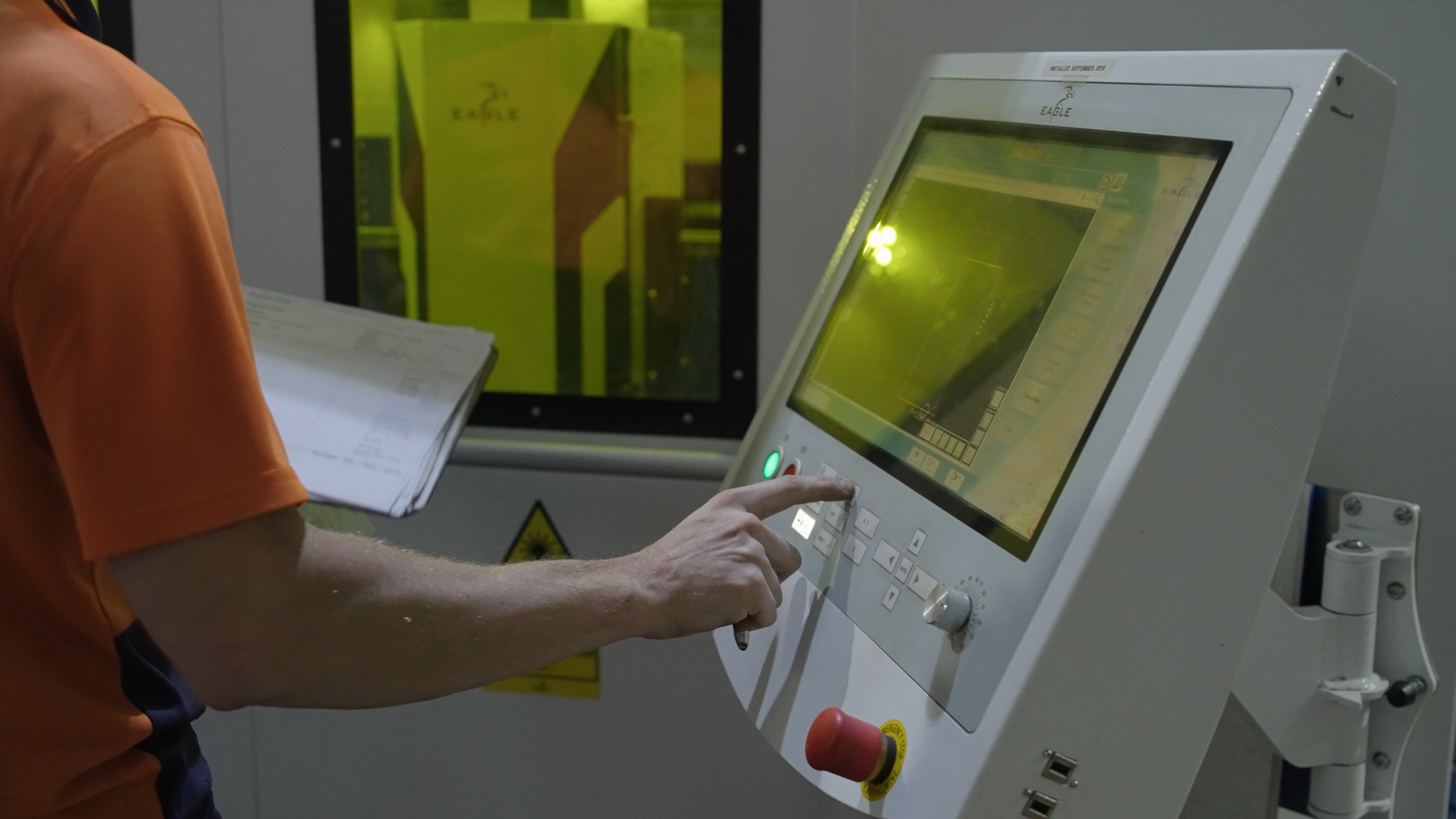
"While our old CO2 laser would run non-stop for eight hours, cutting only two or three sheets of thicker material, the Eagle was initially used for all the fiddly, thin bits and various materials. Now, we do all our cutting on the Eagle. It handles bigger sheets while we load smaller ones, allowing continuous cutting. We swap between sheets seamlessly, cutting faster on thicker material"
“The Eagle is about 30% faster with mild steel and seven to eight times faster with aluminum and stainless steel compared to the CO2 laser. Additionally, the CO2 is more expensive to run, consuming more gas and power even when idling than the Eagle does at full power. Since installing the Eagle, the business has grown by about 20% each year”.
Building a Community: Collaboration Among Eagle Users
A community of Eagle users is growing Down Under: “We frequently connect with other laser cutters, especially those who also use Eagle lasers. Despite the distance between us, we share common interests and assist each other with cutting parameters. If someone is having trouble cutting a certain thickness, we’ll share photos of our settings to help them out, and we receive the same support in return. We often collaborate, especially when dealing with specific materials like 25mm stainless steel 316."
Service and support have also been notable. “Any breakdowns with the old laser were quite expensive. Being in a small country town means service technicians aren't nearby. If we had a problem, even if they flew up, it was pretty much 80 hours. Today, a quick phone call to our service guys gets Eagle involved. They typically dial in from Poland around 6 PM our time and fix the issue in minutes. We've never encountered a problem they couldn't solve remotely. In the rare case, that we needed onsite help, they resolved it quickly and got us back online. We've had the Eagle laser for about five years without any major breakdowns, making it a very reliable machine."
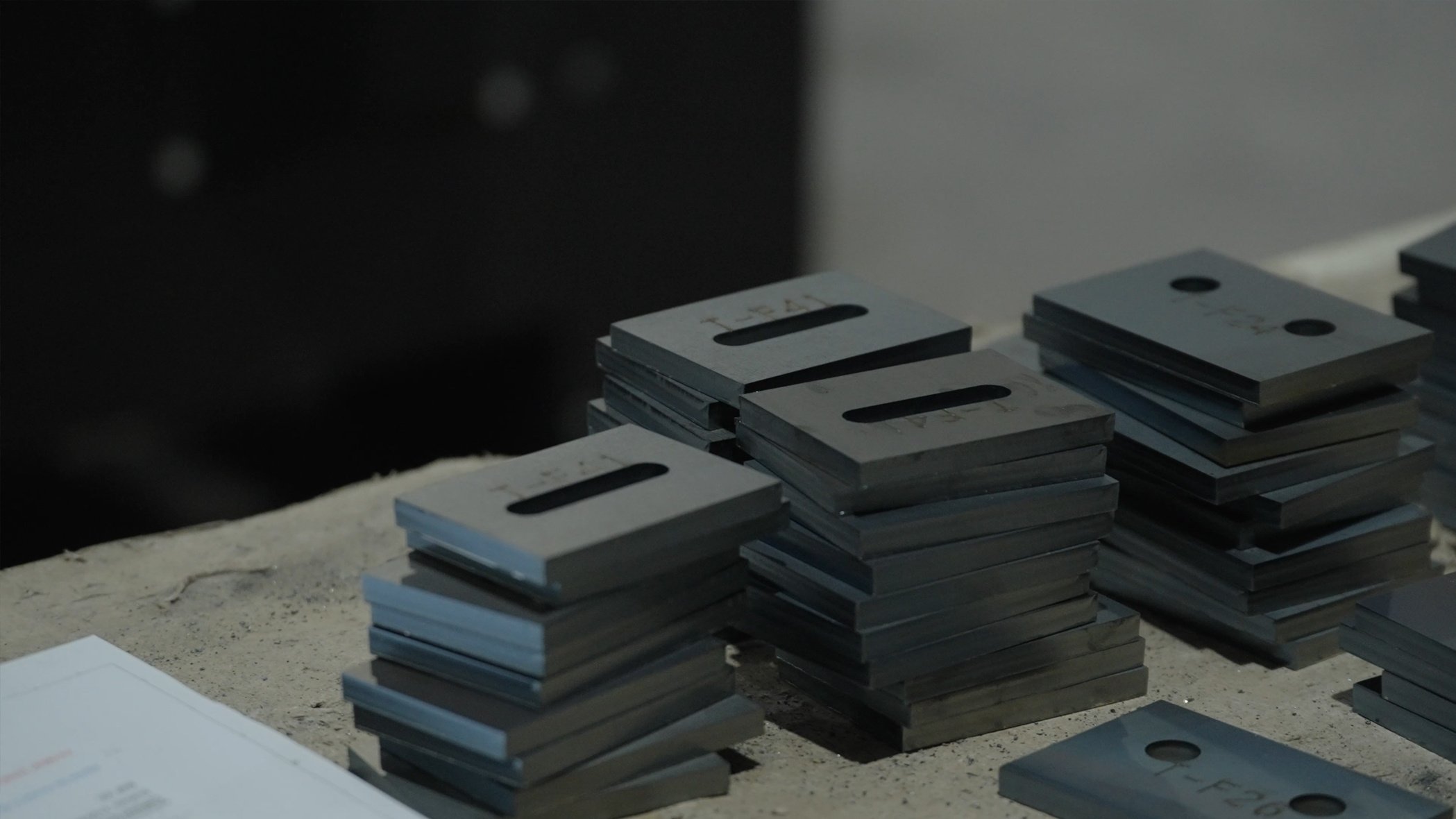
Rodney praises Kraftech, the Australian dealer for Eagle. "Kraftech has been a fantastic business to work with. Andrew, in particular, is a genuine and reliable person. We met him at the EuroBLECH show in Germany, and everything he promised about the warranty and machine was delivered when it was installed. He’s a good, genuine guy and Kraftech is a trustworthy company. They helped explain available options and provided quotes for any configurations we wanted. I highly recommend them."
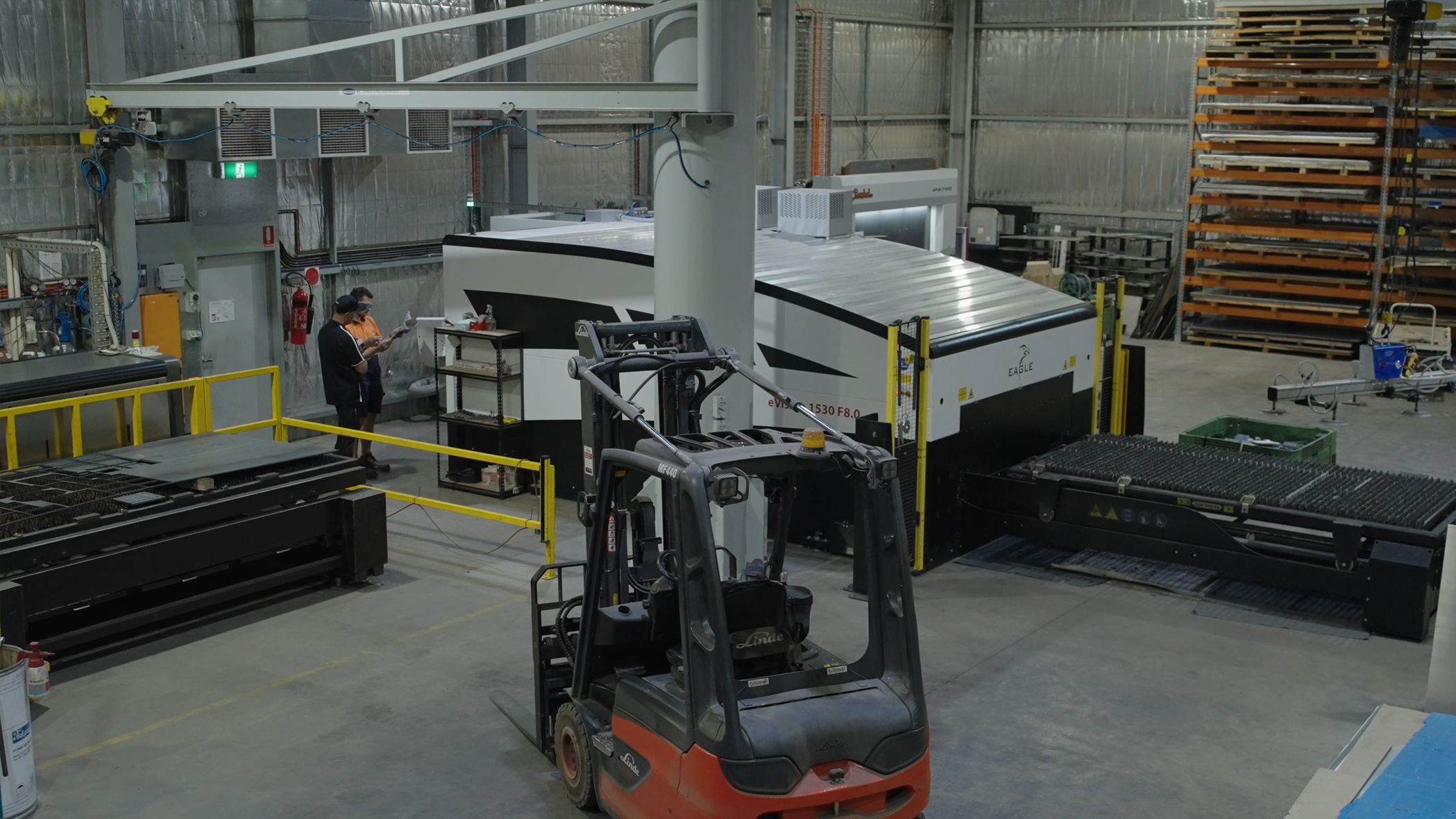
The installation of the Eagle laser took about three days, including setup and final touches. “Once operational, Eagle provided excellent training, which was invaluable for our team. For the next few months, I could contact the technician directly with any questions, which was helpful, even for some of the more basic queries I had”.
“I like the design of the machine. It’s sleek and visually appealing, and you don’t have to worry about hitting your head. Many lasers today look like plain boxes, but the Eagle stands out with its stylish design without being cumbersome. Plus, if we need to access the interior for maintenance or a thorough annual cleaning, we can easily remove the roof for better access and visibility”.
Looking ahead, Mildura Laser is considering a 20kW Eagle fiber laser for even faster cutting of thick materials. Rodney is confident in recommending Eagle: “They’ve been fantastic to work with, and their machines have been excellent."