Driven by innovation: Laserpoint and sheet metal machining
The Candiotto family has been in the sheet metal industry in Villa del Conte, in the province of Padua, since 2005. In the beginning, their company, Laserpoint, was dedicated exclusively to laser cutting. However, responding to market demand and expanding their expertise, new carpentry processes were introduced to meet the growing needs of customers.
The original artisan enterprise run by the family has transformed into a company that has experienced significant growth over the years. This success is evidenced by the move to new premises and the adoption of state-of-the-art machinery in the production process, always aligned with emerging technologies. Prominent among these is an Eagle iNspire 2040 8kW, with CraneMasterStore automation system and supporting eTower.
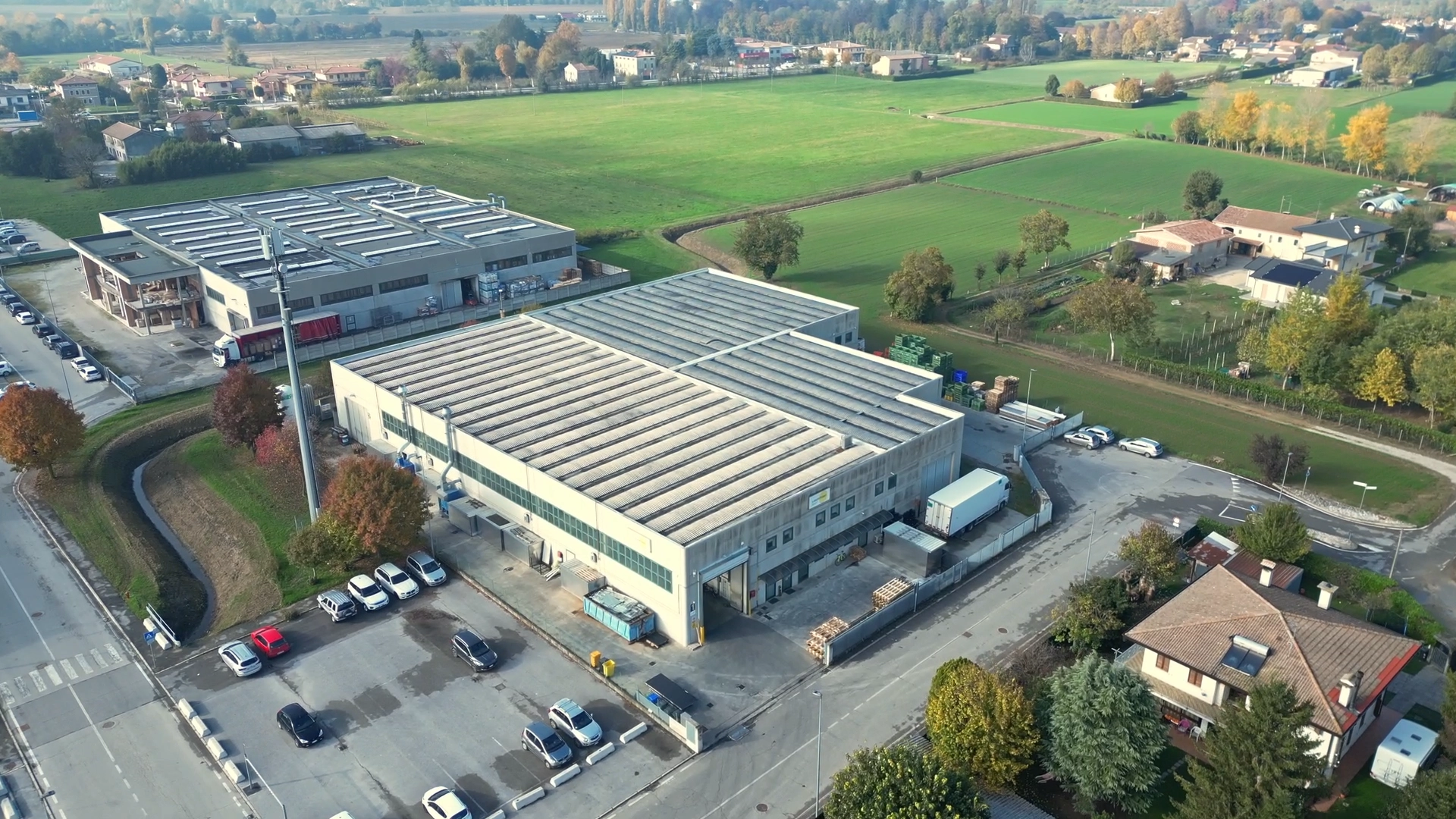
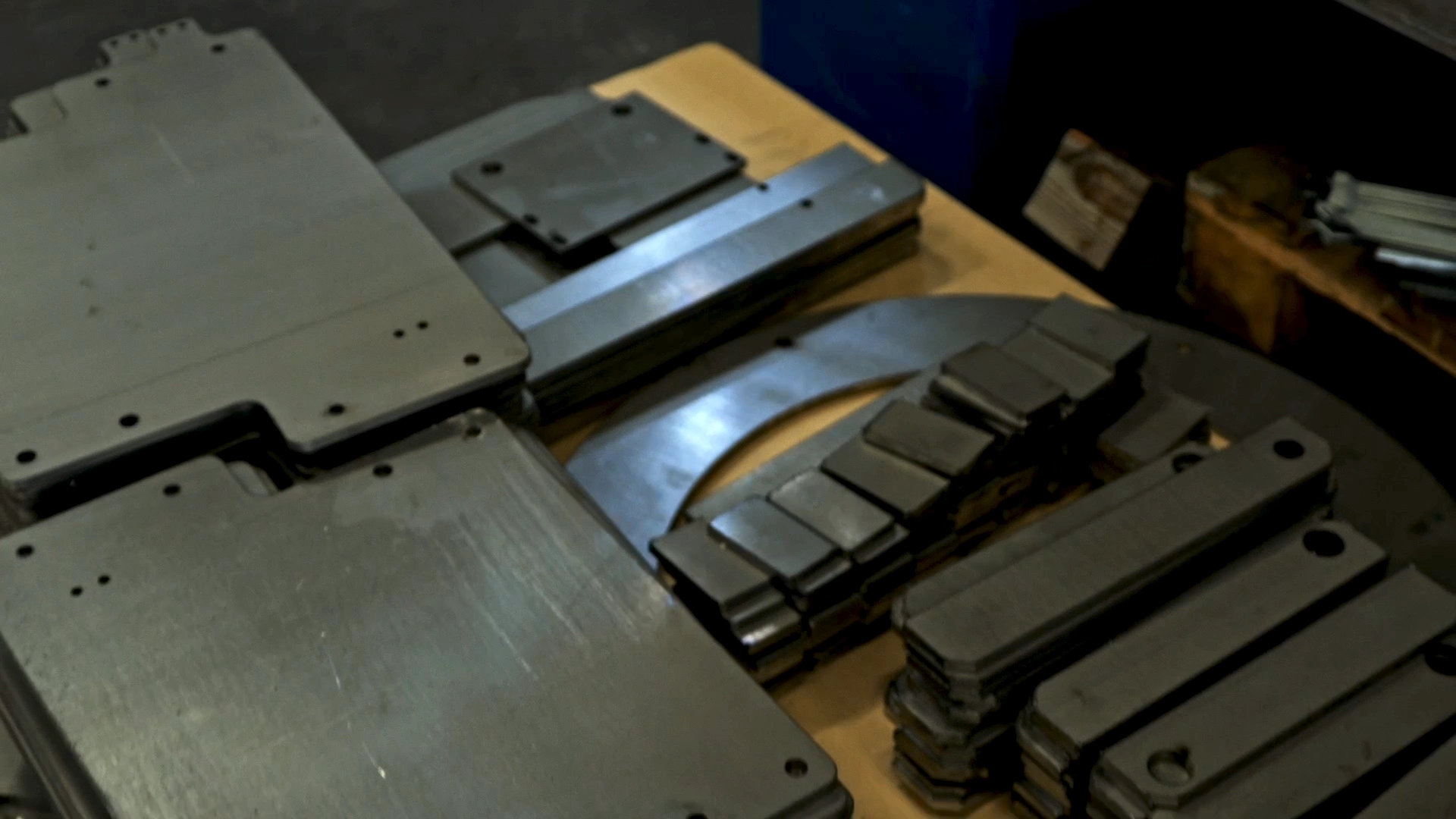
Quality and versatility: the heart of Laserpoint's philosophy
"Currently, we count on a team of 44 dedicated talents and specialize in sheet metal machining, which includes cutting, bending and welding. Our facility consists of three plants, with a total area of about 7,000 square meters," says owner Vasco Candiotto. "We stand out for our versatility: we do not have a specific market, but we operate in a wide range of sectors, from agricultural and food products to furniture and much more. In a nutshell, we adapt to any challenge that comes our way, regardless of the sector we belong to."
The encounter with Eagle’s fiber laser has helped the company maintain a competitive position in the marketplace, ensuring that customers receive products and services that always meet their expectations. "Our ability to work with a wide range of materials is one of our strengths: we competently handle steel, iron and a variety of other materials, with thicknesses ranging from 0.3 mm up to 25 mm," Vasco continues. "This is possible because of the state-of-the-art technology we have adopted. We recently acquired Eagle's laser machine, which has considerable power for our needs, enabling us to process specific materials and thicknesses in an extremely competitive manner."
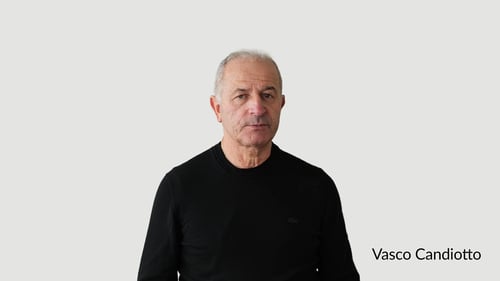
"We chose Eagle as our main supplier for several reasons, but mainly because of the quality of the material it produces and its reliability. During the decision-making process, we focused on the quality aspect, which I think is fundamental. The machine's performance is remarkable: before, with other machines, we could not perform some particular machining operations because of technical limitations. For example, sharp-edged cuts or racks require extreme precision. However, with Eagle, even in the most extreme situations, we have been able to achieve satisfactory results."
Automation: the step up to maximize performance
For such a flexible company, machine power and speed were not enough. A high-performance machine can only reach its full potential if it is combined with an automated material handling system. As Vasco Candiotto explains, "Laserpoint collaborates with companies from different sectors, which means we can find ourselves having to change thicknesses up to 7-8 times a day. Thanks to the automation tower, we can manage this process without downtime, as the materials we need are already loaded. This flexibility is critical for us and allows us to maintain a high level of productivity. Without automation, it would be unthinkable to effectively manage our production."
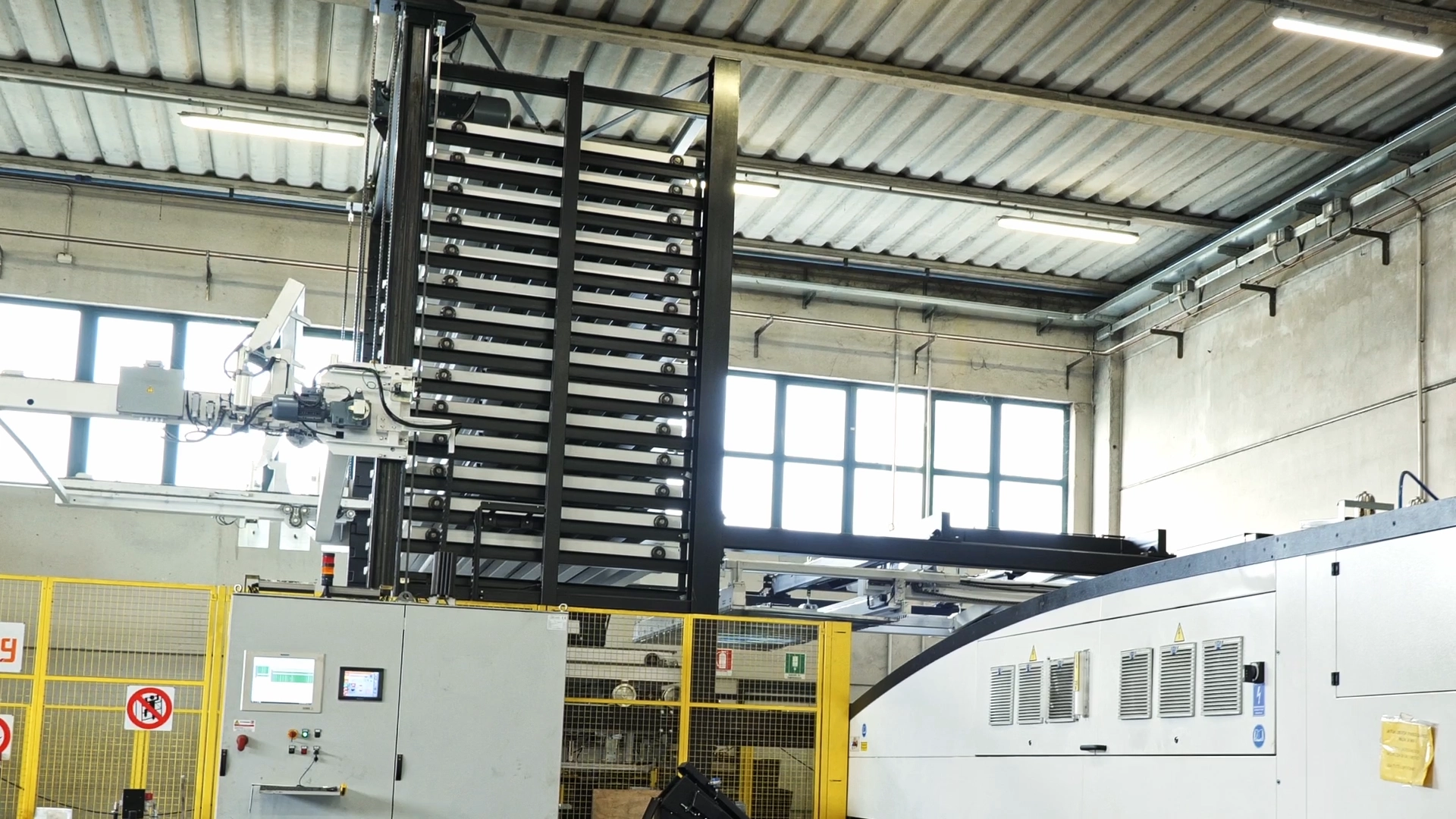
Monitoring and support: service is key for continued productivity
With its in-house engineering department, Laserpoint offers customers the ability to implement a wide range of projects quickly. Starting with conceptual development using three-dimensional programs, we proceed with simulations on the machines and finally find the solution that fully satisfies the customer. Special attention is paid to details and quality, both of the raw material and subsequent processing, ensuring a high-quality product.
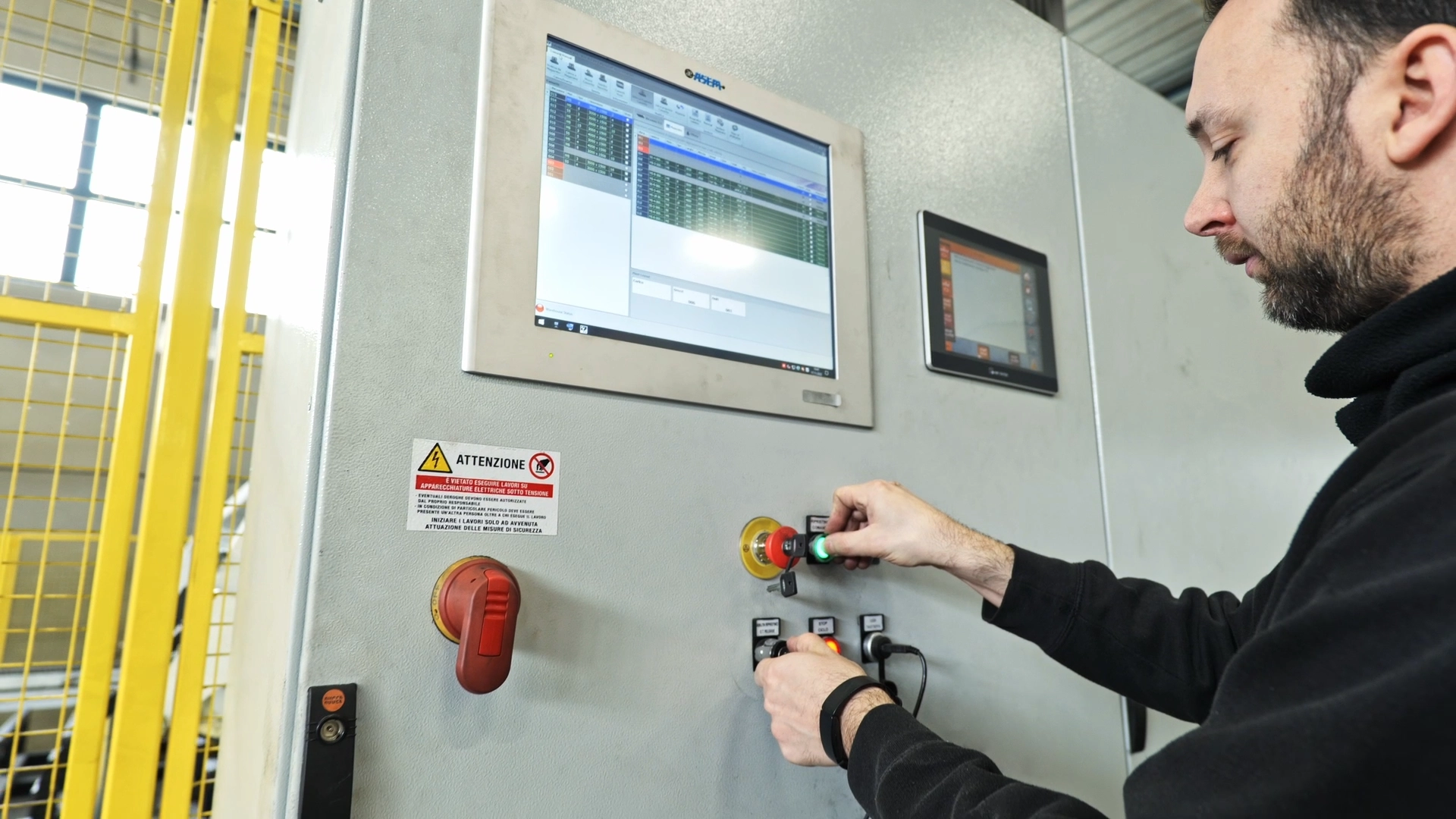
"From the office, we can monitor the process in detail: we can see whether a part is being welded, where it is in production, or whether it has already been unloaded from the machine. The monitoring program is interfaced directly with Eagle and runs smoothly, thanks to close cooperation with the company's technicians," he concludes. "We cannot complain about the support we received: although we initially had some hesitation about the availability of technical support, after three years of use we can confirm that our concerns were unfounded. In addition, the presence of several Eagle machines in the area has provided us with additional peace of mind."